Laser Process Fortifies Metals Extending Component Life Tenfold
The continual demand for greater material strength, durability, and longevity in structural applications makes metal a constant focus and challenge for material scientists and engineers. One of the best ways to modify the mechanical and structural properties of metal is through peening, a process that uses surface impaction to produce permanent, compressive residual stress layers within a metal’s surface; once the external impact stress dissipates, the peened material retains its harder, more durable quality. Contemporary peening processes used round metallic or ceramic balls to compress a material and harden its surface. Though this process works, shot peening has less-than-exact control due to the nature of ballistic balls, the limited or sub-surface impaction depths, and the prevalence of pitting throughout the target surface material. To combat these limitations, Metal Improvement Company (MIC)—a subsidiary of Curtiss-Wright Surface Technologies—and LLNL partnered to develop the commercial production of a more efficient method to strengthen metal: laser peening.
Although laser peening technology existed in the 1960s, its irregularity undermined the technology’s commercial viability. That is, until LLNL began applying its high-energy, high-repetition-rate, short-pulse laser to peening applications in the 1990s. Since laser-based peening allows for precision control and compaction depths of 5–10 times deeper than shot peening, a perfected laser-peeing process would expand potential applications from gears, coils, and crankshafts to more structurally demanding items such as steam turbine blades, aircraft structures, and high-performance engine components. Leveraging Livermore’s robotic mounts for fast, customized, computer-controlled peening angles, laser peening soon acquired the characteristics of speed, efficiency, and consistent coverage to warrant commercial development. Shot-peening industry leader MIC funded additional research at LLNL to hone the short-pulse laser technology for laser peening and subsequently licensed the patent portfolio covering the LLNL laser system. MIC opened its first laser peening facility in 2002 and now has three peening facilities in the US, one in the UK, and mobile peening systems with the capability to go on-site anywhere in the world.
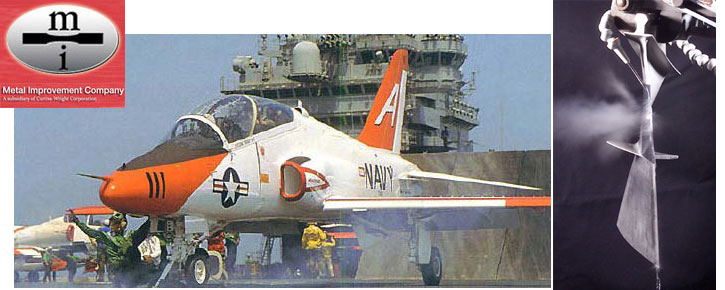
The commercial laser peening process developed by LLNL and MIC extends the service lifetime of aircraft engines, power turbines, and other critical components of military and civilian systems by a factor of 10. The impacts of this technology are particularly evident in the aerospace industry, where laser peening has improved more than 10,000 jet engine turbine blades and extended the lifespan for components of aircraft for customers ranging from Boeing, Rolls Royce, Siemens, and the Department of Defense. Using LLNL’s technology, MIC now treats blades for steam and gas turbines for all major electric power equipment manufacturers in the U.S.
MIC integrated LLNL-developed laser technology and peening capability into a viable commercial process that continues having a major global impact. Laser peening improves performance, increases service life, and reduces costs for various industry structures and propulsion, yielding billions of dollars in savings for jet engine fan blades, fuselages, wings, and other components of civil and military aircraft structures, electricity generation steam turbines, and high-performance racing vehicles.