Lawrence Livermore National Laboratory is a leading new chemicals and materials creation with a broad array of applications including batteries, catalysts for clean technology, ceramics, composites, additives and more. The Lab’s unique Advanced Manufacturing capabilities go hand in hand with the creation of novel methods to create new concepts altogether.
Portfolio News and Multimedia
The trade journal R&D World Magazine recently announced the winners of the awards, often called the “Oscars of innovation,” recognizing new commercial products, technologies and materials that are available for sale or license for their technological significance.
Lawrence Livermore National Laboratory (LLNL) scientists and engineers have earned four awards among the top 100 inventions worldwide. With this year’s results, the Laboratory has now collected a total of 186 R&D 100 awards since 1978.
Submitted through LLNL’s Innovation and Partnerships Office (IPO), these awards recognize the impact that Livermore innovation, in collaboration with industry partners, can have on the U.S. economy as well as globally.
A multidisciplinary team of researchers at Lawrence Livermore National Laboratory (LLNL) developed a new type of electrically controlled, near-infrared smart window that can cut near-infrared light transmission by almost 50%. Their secret ingredient? Vertically aligned carbon nanotubes—tiny, tube-shaped structures made from carbon atoms that are thousands of times thinner than a human hair. The research was published in Nano Letters.
Information about the opportunity to license the technology can be found here: Electrochromic Devices Made from VACNTs
A recording of DOE Office of Technology Commercialization's National Lab Discovery Series webinar that introduces TAOS — The Alloy Optimization Software was recently posted. Discover how Lawrence Livermore National Laboratory is making metal alloy design faster, easier, and more accessible with TAOS.
TAOS is a cross-platform tool that helps users design new alloys based on target properties like melting temperature or phase stability — without requiring deep expertise in materials science. With an intuitive interface and powerful back-end modeling, TAOS allows users in aerospace, automotive, power generation, electronics and more to screen large multicomponent systems in minutes using a standard computer. This enables non-experts to develop new complex metal alloys for unique industrial applications in an accelerated, flexible and cost-efficent way. To learn more about TAOS, go to LLNL's software portal.
Chemicals and Materials Technologies
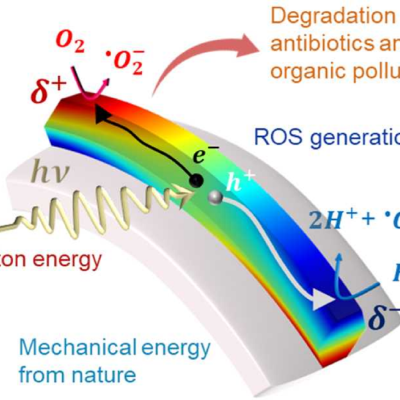
LLNL researchers have introduced the use of a kirigami inspired substrate to act as a mechanical transducer, which converts macroscale stretching motion into localized bending. The performance of photo-piezocatalysts made with aligned arrays of photocatalytic nanomaterials on the kirigami shaped substrate yields significant enhancements (~250%) in the degradation of dyes.
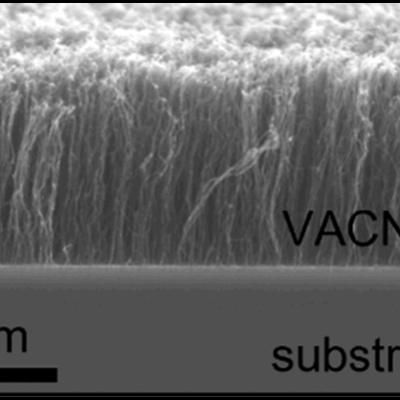
LLNL inventors have developed an electrochromic device containing Vertically Aligned single walled CNTs (VACNTs) with a range of diameters. The assembly of these devices into electrochromic windows filled with ionic liquid allows for reversible modulation of the Fermi level in the VACNT film. These electrochromic devices show strong voltage-dependent transmission of near-infrared…
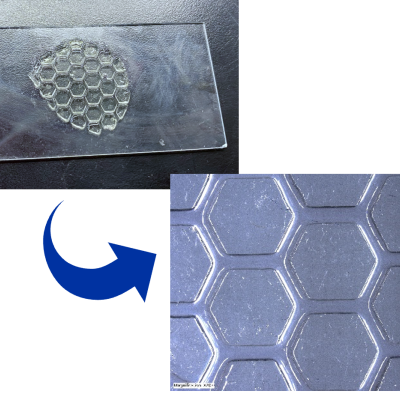
LLNL inventors have developed a photopolymer resin formulation that consists of a (1) pH labile monomers, (2) a photoinitiator, (3) a photoacid or photobase generator, (4) other additives including, reactive and unreactive diluents, and pH stabilizers. When exposed to radiation in a specific wavelength region, component 2 initiates polymerization with 1 to form a pH sensitive network.…
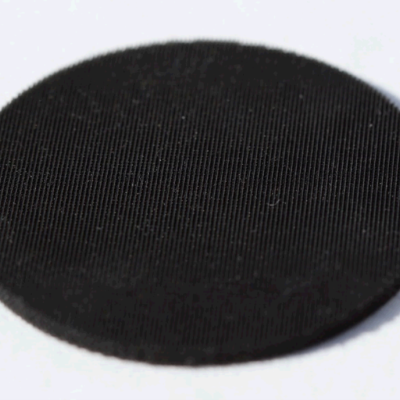
LLNL researchers have developed a silicone based conductive, elastomeric 3D DIW printed structure with a lower wt.% conductive, composite filler to allow for the creation of 3D printed lattice structures with tunable conductivity. The conductivity of the printed structure can be varied using composition of the starting DIW ink formulation as well as the 3D printed spacing and…
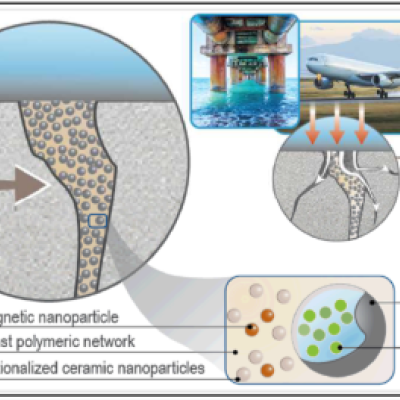
LLNL researchers are developing Concrete Assisted by Particles Sealed Under Large-scale Encapsulation (CAPSULE) to provide a solution that utilizes different biological and engineering approaches to repair aging concrete. It uses an innovative method to
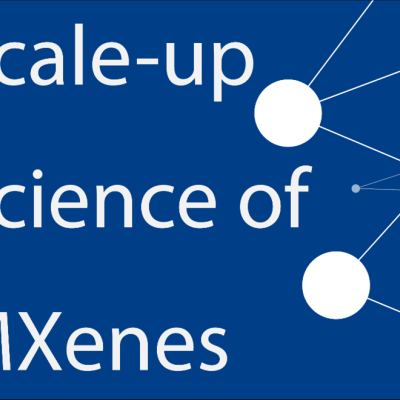
To address these challenges and explore the scale-up science of MXene, LLNL researchers have developed a scalable solution-phase synthesis method to generate MXene with over 70% production yield via top-down exfoliation approaches with non-aqueous solvents and salts. The novel method is a dramatic improvement compared to conventional approaches (10-20%). Furthermore, the shielding…
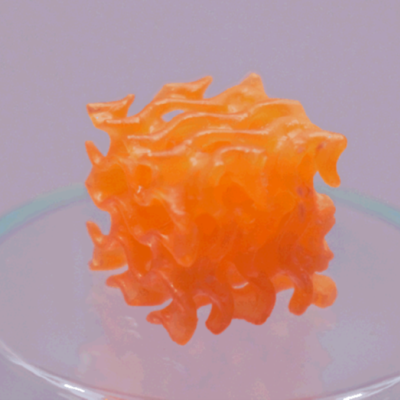
LLNL researchers have developed a method which utilizes functional alcohols to depolymerize polyurethane crosslinked networks. The functional alcohols show 5X increase in the depolymerization efficiency compared with current state of art (e.g. methanol, ethylene glycol). The crosslinked polyurethane networks completely depolymerized into a liquid oligomer within 48 hours at ambient…
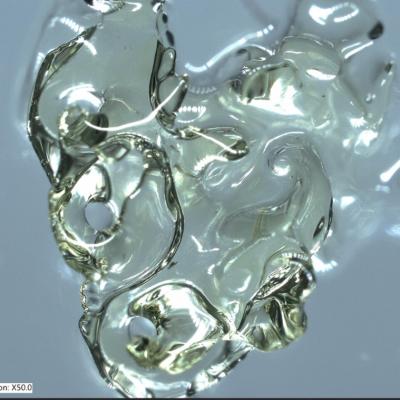
LLNL researchers have developed a novel photocurable silicone useful for producing three-dimensional objects via additive manufacturing. The resin formulations consist of a mult-component siloxane polymers with different functionalities, a platinum catalyst, a photoinitiator, and other organic peroxides. The LLNL invention involves controlling the spatial and temporal aspects of the…
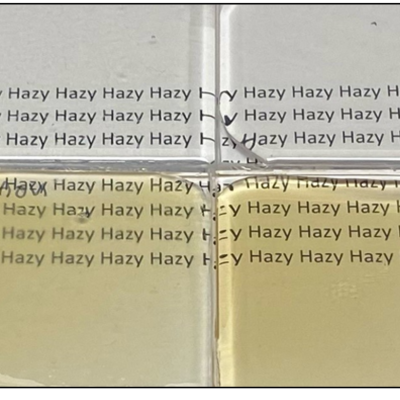
LLNL researchers have created a suitably compliant adhesive that is based on a thiol monomer mixed with an epoxy monomer in the presence of metal oxide nanoparticles. When cured into films or pucks, the adhesives are optically transparent with a RI up to ~1.68 at 532 nm with varying shore A hardness in the range of 50 to 98. The adhesive can potentially be mixed and potted between Ti:…
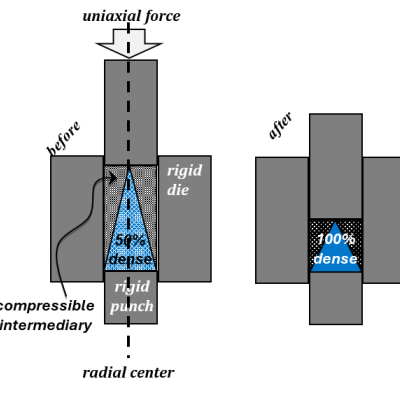
LLNL has developed a novel Production of Readily compressible dies for Enhanced Sintering of Solids (PRESS) method for ceramic parts manufacturing that uses compressible, non-sintering powder materials as a mold which can match the compaction of the ceramic powder starting materials during pressure-assisted sintering. PRESS enables uniform deformation of the part under a constant linear travel…
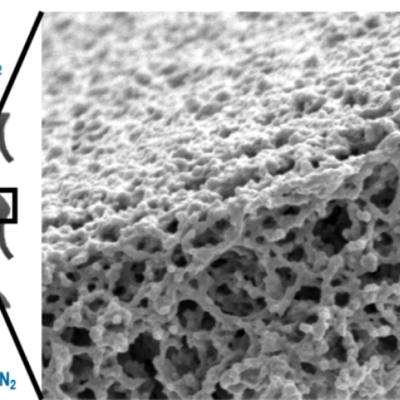
LLNL researchers have developed a self-supporting structural material that promises more efficient carbon capture specifically from air, but generally from all CO2 containing gas sources. The material is produced with a liquid high-amine-content precursor polymer that is functionalized by adding on polymerizable end groups.
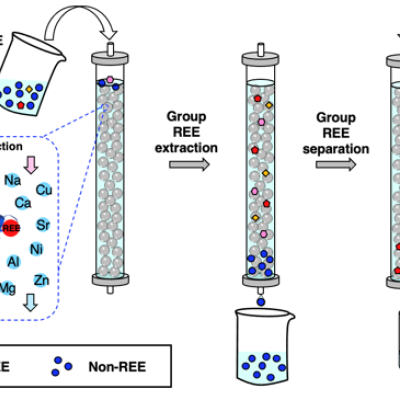
As an important step toward overcoming the technical and environmental limitations of current REE processing methods, the LLNL team has patented and demonstrated a biobased, all-aqueous REE extraction and separation scheme using the REE-selective lanmodulin protein. Lanmodulin can be fixed onto porous support materials using thiol-maleimide chemistry, which can enable tandem REE purification…

LLNL researchers have developed two approaches to fabricate nanocrystal superlattices for electronic and optoelectronic devices. Nanocrystals covered by this approach include, but are not limited to, metal nanocrystals, semiconducting nanocrystals (quantum dots), and insulating nanocrystals, or a combination of those.
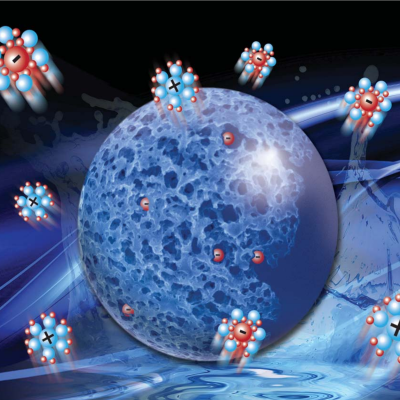
LLNL has a long history of developing aerogels. Because of their high surface area, they have unique physical, chemical, and mechanical properties, which makes aerogels a promising material for use in a variety of technical applications areas ranging from energy storage to catalysis. LLNL researchers are able to tailor the structure and properties to create strong, high-density…
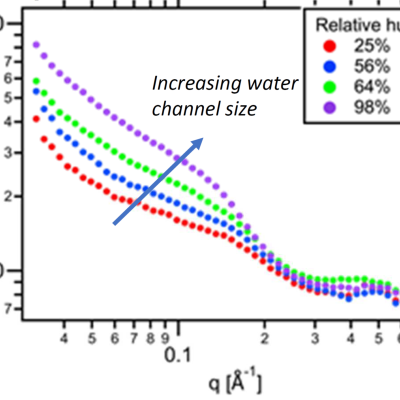
LLNL researchers have developed a method to enhance the performance of polyelectrolyte membranes by using a humidity-controlled crosslinking process which can be applied to precisely adjust the water channels of the membrane.
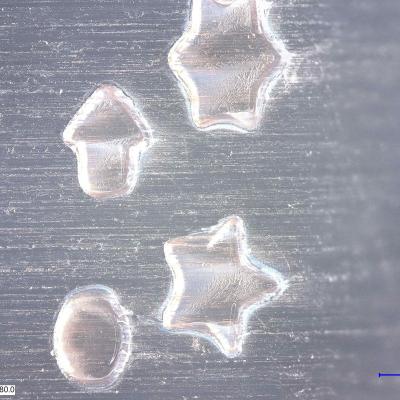
LLNL’s invention is a photopolymerizable polymer resin that consists of one or more nitrile-functional based polymers. The resin is formulated for SLA based 3D printing allowing for the production of nitrile-containing polymer components that can then be thermally processed into a conductive, highly graphitic materials. The novelty of the invention lies in (1) the photo-curable nitrile-…
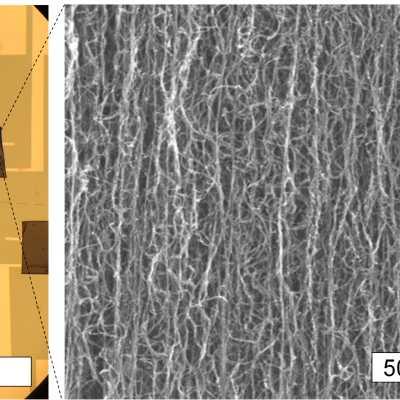
LLNL researchers has devised several design strategies to enable gating of thick architectures (e.g., 2D planar, 3D out-of-plane) made of nanostructures while maintaining substantial surface area available for sensing. Specific examples described in the patent application (2021/0249618) are given for carbon nanotubes (CNTs) and including typical channel gate configurations, gate-all-…
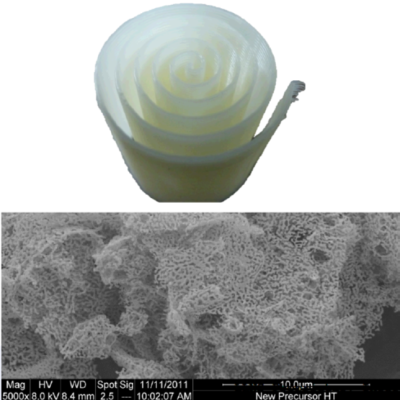
LLNL researchers developed a novel method in preparing the ceramic nanofibrous material, which are used to attract and hold particles as well as unique filter designs. The ceramic fibers are prepared via electro spinning to make sheets of nanofibers. The sheets can then be formed into tubes of high surface area.
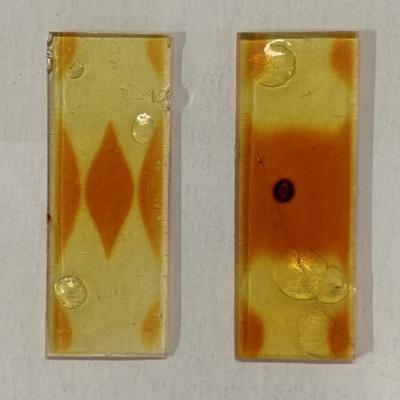
LLNL researchers have developed an innovative and uniform single-pot polymer multi-material system, based on a combination of 3 different reactive chemistries. By combining the three different constituent monomers, fine control of mechanical attributes, such as elastic modulus, can be achieved by adjusting the dosage of UV light throughout the additive manufacturing process. This…
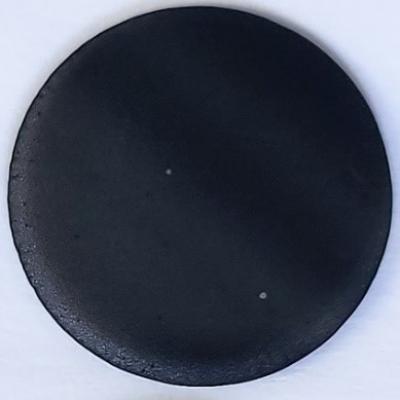
LLNL researchers have developed a method to incorporate gas phase synthesized graphene (GSG) as a unique additive in a UV-crosslinkable polymer formulation. The GSG is added by using a planetary mixer to obtain a homogenous suspension of GSG in polymer. The resulting formulation is highly stable and doesn't show signs of phase separation or solid sedimentation. The polymer formulation is then…
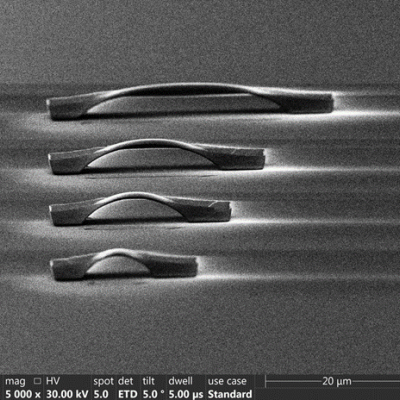
LLNL researchers developed a novel method to nucleate the alpha phase of Tantalum on a polymer surface at room temperature, allowing for the controllable formation of a variety of 3D structures, such as airbridges. Using this method with a subsequent Piranha etch results in the complete removal of the residues of the polymer 'scaffolding' or template while allowing the deposited tantalum…
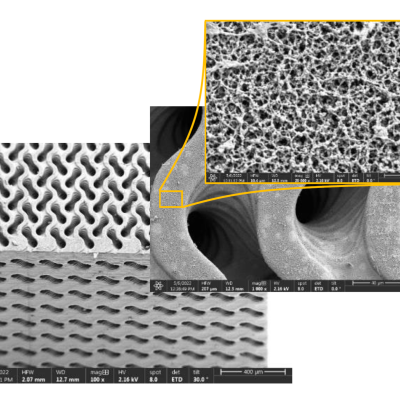
LLNL researchers have developed novel advanced manufactured biomimetic 3D-TPMS (triply periodic minimal surface) membrane architectures such as a 3D gyroid membrane. The membrane is printed using LLNL's nano-porous photoresist technology. LLNL’s 3D-TPMS membranes consist of two independent but interpenetrating macropore flow channel systems that are separated by a thin nano-porous wall…
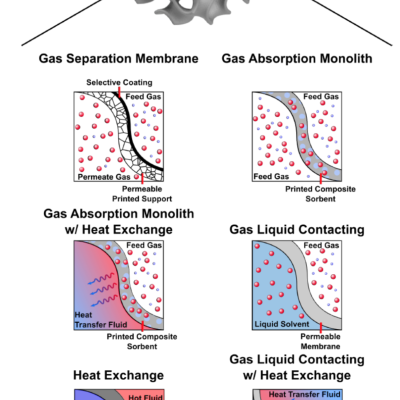
LLNL researchers have devised a set of design principles that facilitates the development of practical TPMS-based two fluid flow reactors.; included in the design are these new concepts:
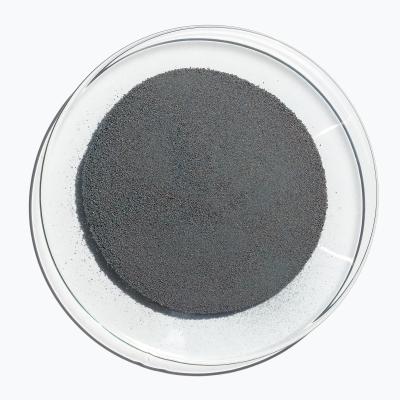
LLNL researchers have developed a Li-Sn-Zn ternary alloy and its method of production. Instead of traditional alloying techniques, the alloy was synthesized using mechanical alloying (high energy ball milling). With high purity elemental powders of lithium, tin and zinc, LLNL researchers were able to prepare Li60Sn20Zn20 as well as Li70Sn20Zn10 nanopowders.
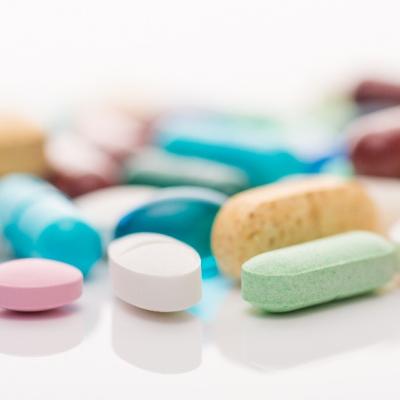
LLNL researchers have developed a technology suite that includes several methods for detecting trace levels of illicit drugs even in mixtures. These methods can be used as a rapid screening test for incoming samples; for the samples that were determined to contain detectable amounts, they would undergo final verification using conventional laboratory analytical techniques.
![Filled (8,8) (left) and (15,15) (right) CNTs with [EMIM+][BF4- ] using SGTI with the proposed spliced soft-core potential (SSCP) approach](/sites/default/files/styles/scale_exact_400x400_/public/2023-10/Filled%20CNTs%20using%20SGTI.png?itok=Dy0ObN7i)
LLNL researchers have developed a novel simulation methodology using slow growth thermodynamic integration (SGTI) utilizing spliced soft-core interaction potential (SSCP). The approach to filling the molecular enclosures is a nonphysical one. Rather than filling the pores from the open ends this method creates steps in the algorithm that allow molecules to pass through the pore…
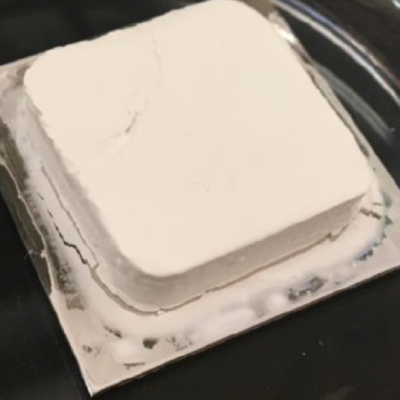
LLNL researchers have developed a method to manufacture solid standard reference materials (SRMs) that can be used as calibration standards for elemental and isotopic analyses. The novel method allows for the growth of compositionally controlled particles as starting materials, and the synthesis of SRMs with single or multi-component(s) through electrophoretic deposition (EPD). The SRMs are…
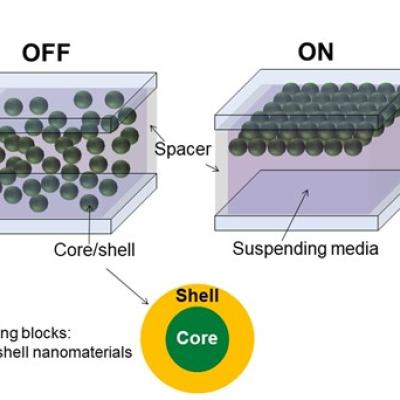
LLNL inventors have shown that the optical material properties (transmission, reflectance, color) of an assembled device can be dynamically tunable using innovative core-shell nanomaterials and a structured composite crystal/colloid design. These smart optical materials are assembled from nanosized constituents that have a native surface charge. The nanoparticles can be manipulated by an…
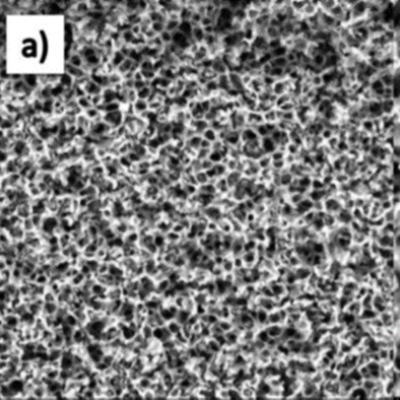
LLNL inventors have created innovative steps in the synthesis, carbonation and activation steps of aerogel manufacturing that allows for large scale production. These steps are:
1. Synthesis: a novel pre-cure step with subsequent gelation (RF precursor solution is heated with stirring to achieve a mixed liquid intermediate temperature, the precursor solution is then allowed to cool,…
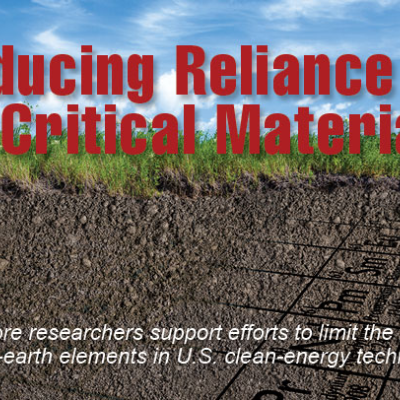
CMI—a DOE Energy Innovation Hub—is a public/private partnership led by the Ames Laboratory that brings together the best and brightest research minds from universities, national laboratories (including LLNL), and the private sector to find innovative technology solutions to make better use of materials critical to the success of clean energy technologies as well as develop resilient and secure…
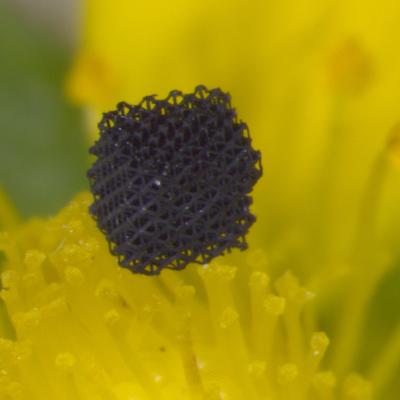
To overcome challenges that existing techniques for creating 3DGs face, LLNL researchers have developed a method that uses a light-based 3D printing process to rapidly create 3DG lattices of essentially any desired structure with graphene strut microstructure having pore sizes on the order of 10 nm. This flexible technique enables printing 3D micro-architected graphene objects with complex,…
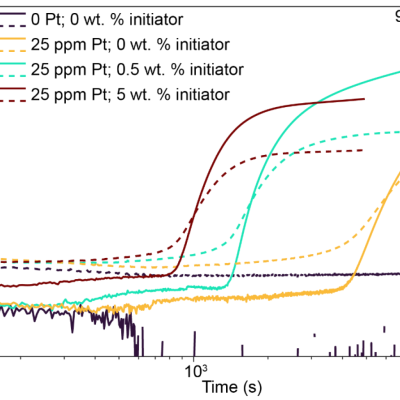
The approach is to use peroxides to modify the reaction kinetics in the production of polysiloxanes. A radical initiator in the presence of a hydride-terminated polysiloxane will increase the rate of curing and reduce manufacturing costs. At a minimum a formulation would contain a hydride-terminated polysiloxane, a platinum catalyst, and an initiator that generates radicals. …
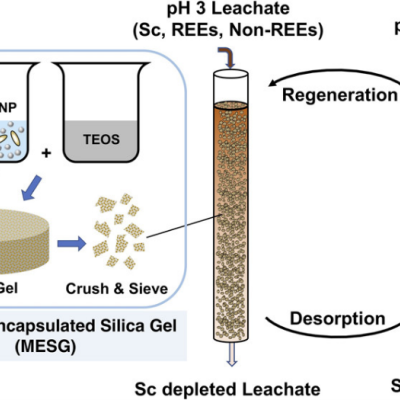
The novel technology developed at LLNL is a new, effective means of separating and concentrating Sc from lanthanides and non-REEs in unconventional, waste-derived feedstocks, thereby transforming an essentially valueless solution into valuable Sc concentrates. The results represent an important advance in the development of an environmentally sustainable alternative to organic solvent-…

LLNL researchers have discovered that some inexpensive and commercially available molecules used for other applications, could render certain lanthanide and actinide elements highly fluorescent. These molecules are not sold for applications involving the detection of REEs and actinides via fluorescence. They are instead used as additives in cosmetic products and/or in the pharmaceutical…
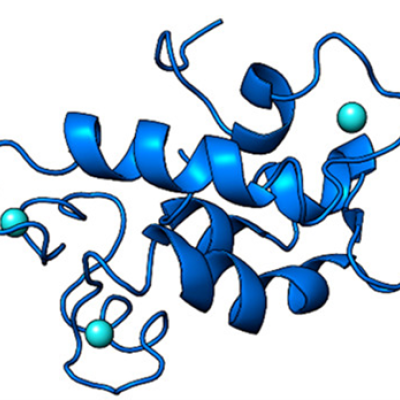
LLNL researchers along with collaborators at Pennsylvania State University have found that a newly discovered natural protein named Lanmodulin (LanM) could be a potential candidate for extracting REEs from ore or other sources such as coal ash as well as purifying the REE material. Through joint research, the scientists found that LanM undergoes a large conformational change in response…
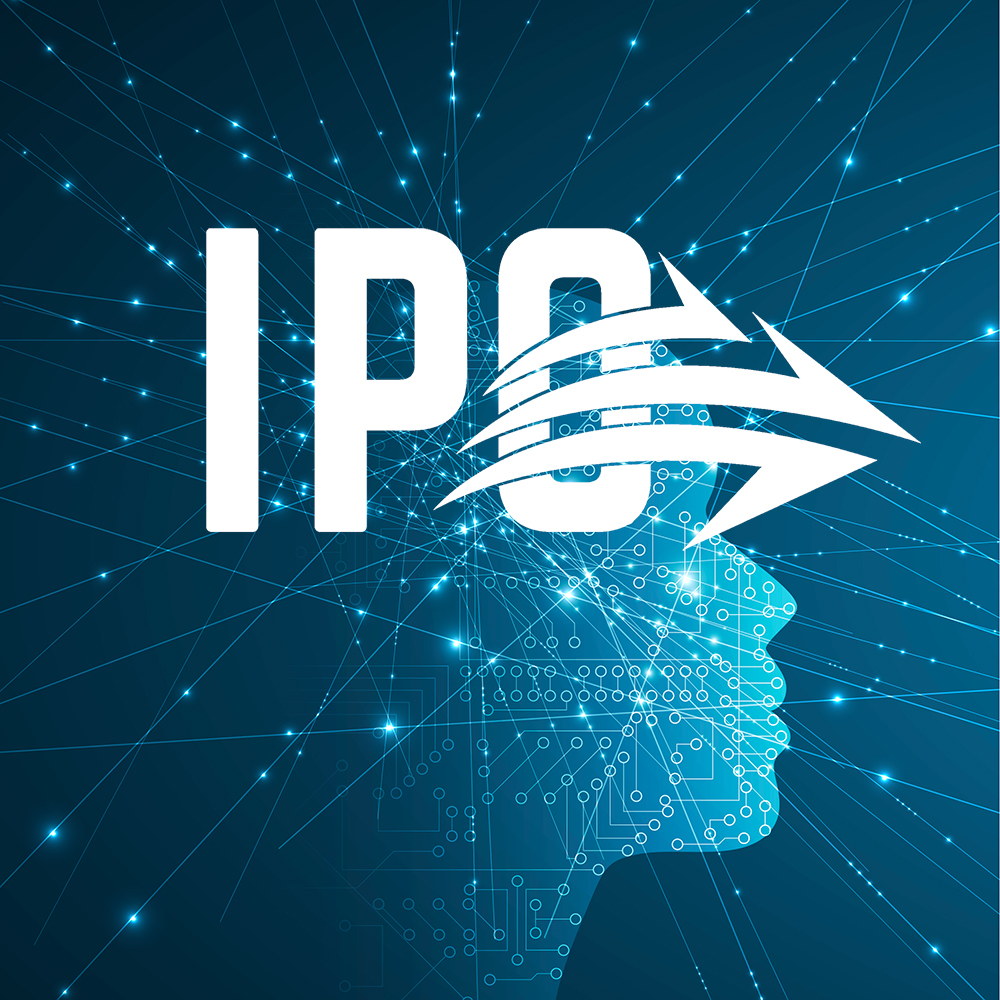
LLNL researchers have developed a custom formulated extreme low viscosity reactive silicone resin base modified with a temperature dependent thixotrope along with a modified catalyst package. The uncatalyzed composition is capable of accepting loadings of polymer microspheres sufficient to produce a cured bulk rubber that has a density as low as 0.3 g/cc, thus compatible with high-…
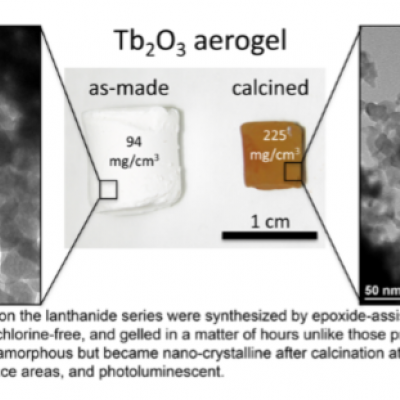
The innovators have modified a epoxide-assisted sol-gel method to produce chlorine-free, monolithic REO aerogels in just a matter of hours. This method was demonstrated for the lanthanide series. An important factor in realizing the sol-gel transition with the nitrate precursor was the addition of a key ingredient and moderate heat.. These alcogels can then be dried and calcined to produce…
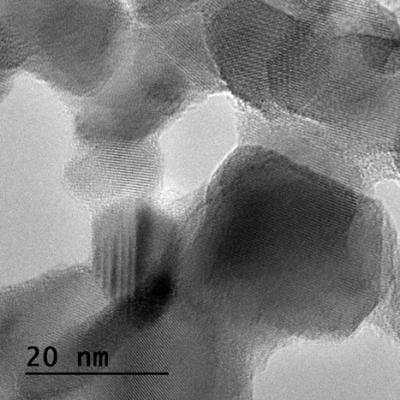
Livermore researchers have developed two novel TiCl4 based non-alkoxide sol-gel approaches for the synthesis of SiO2/TiO2 nanocomposite aerogels. Composite SiO2-TiO2 aerogels were obtained by epoxide-assisted gelation (EAG route) of TiCl4/DMF solution in the presence SiO2 aerogel particles. Additionally, the same TiCl4/DMF solution was employed to prepare SiO2@TiO2 aerogels by a facile one-…
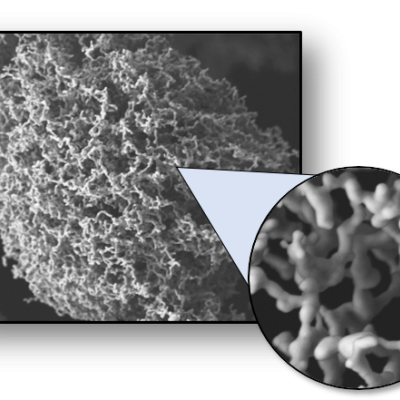
The LLNL method is based on freeze‐casting of aerosolized and pressurized metal salt solutions and subsequent thermal processing. This method generates both porous particles with sizes down to one micron and macroscopic monoliths with nanometer scale ligaments/struts. The material's density can be controlled during the freeze‐dried stage. Compared to conventional approaches, this method…
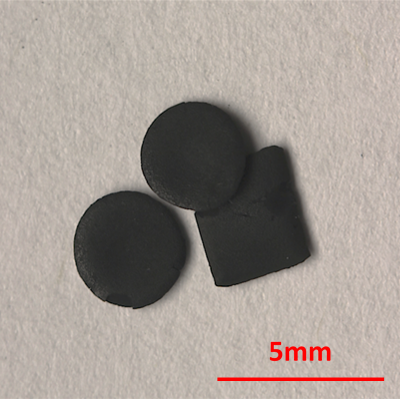
LLNL uses the additive manufacturing technique known as Electrophoretic Deposition to shape the source particle material into a finished magnet geometry. The source particle material is dispersed in a liquid so that the particles can move freely. Electric fields in the shape of the finished product then draw the particles to the desired location to form a “green body”, much like an unfired…
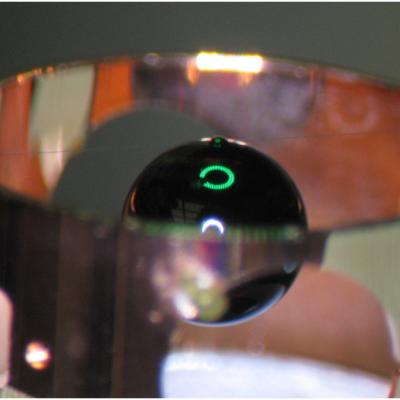
LLNL has developed a liquid-free method that increases the overall mechanical resistance of self-supported, carbon nanotube assemblies through nanoscale reinforcement by gas-phase deposition of a thermally cross-linkable polymer. Polymer-reinforcement increases the strength of CNT yarns after crosslinking. For example, a minimal amount (<200 nm) of poly-glycidyl metacrylate (PGMA) deposited…
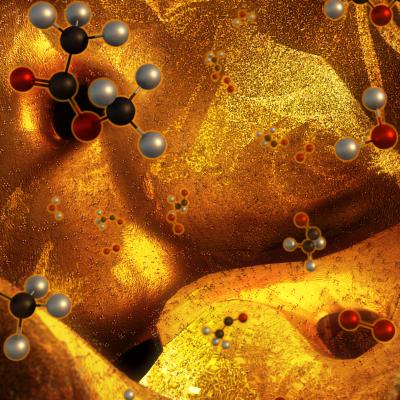
By combining 3D printing and dealloying., researchers at LLNL have developed a method for fabricating metal foams with engineered hierarchical architectures consisting of pores at least 3 distinct length scales. LLNL’s method uses direct ink writing (DIW), a 3D printing technique for additive manufacturing to fabricate hierarchical nanoporous metal foams with deterministically controlled 3D…

LLNL researchers have developed an alternative route to protective breathable membranes called Second Skin technology, which has transformative potential for protective garments. These membranes are expected to be particularly effective in mitigating physiological burden.
For additional information see article in Advanced Materials “Ultrabreathable and Protective Membranes with Sub-5…
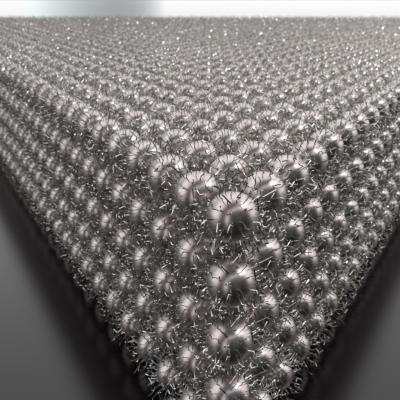
The novel LLNL technique uses electric fields to drive and control assembly. In the literature such methods have heretofore only formed disordered ensembles. This innovative method increases local nanocrystal concentration, initiating nucleation and growth into ordered superlattices. Nanocrystals remain solvated and mobile throughout the process, allowing fast fabrication of ordered…
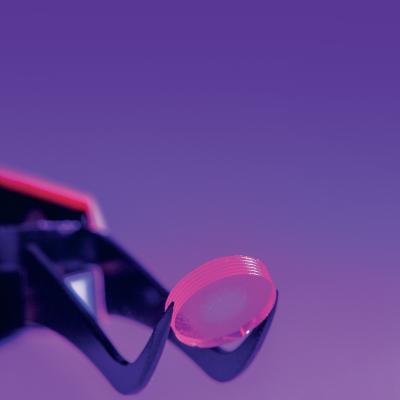
LLNL researchers have developed a custom resin formulation which uses a dispersing solvent and only a multifunctional monomer as the binding agent. The dispersing solvent system typically used has multiple components meant to achieve excellent dispersal of silica in order to create a flowable resin (rather than a paste). The dispersing agent has low vapor pressure, which allows the 3D printed…
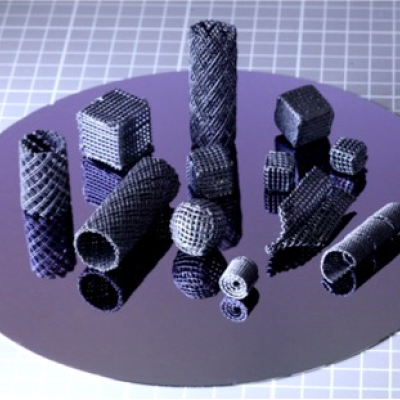
LLNL researchers have developed a novel method of 3D printing regular microstructured architectures and subsequent complex macrostructures from additively manufactured bio-based composite thermoset shape memory polymer composite materials. This technology for 3D additively manufactured parts utilizes up to a 4 axis control DIW system for fabricating bio based thermally cured epoxy based SMP…
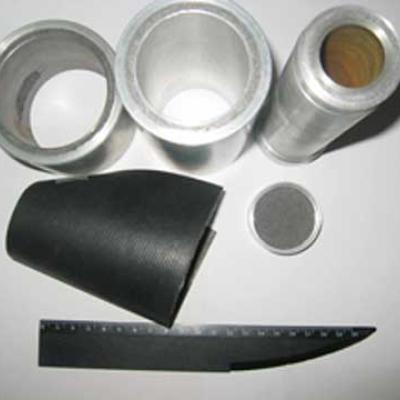
LLNL researchers have developed the hardware and chemistry to allow additive manufacturing of short carbon fibers in a thermoset polymer matrix which have a high degree of structural alignment over conventional cast or pressed short/chopped carbon fiber polymer composites.
The invention is based on the shear dispersal, alignment and concentration of fiber fraction within a resin…

Nanomaterials that are emerging out of cutting edge nanotechnology research are a key component for an energy revolution. Carbon-based nanomaterials are ushering in the "new carbon age" with carbon nanotubes, nanoporous carbons, and graphene nanosheets that will prove necessary to provide sustainable energy applications that lessen our dependence on fossil fuels.
Carbon aerogels (CAs)…
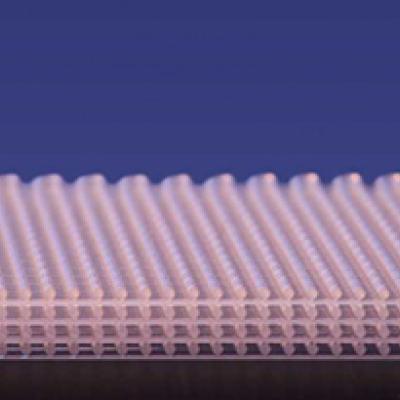
To overcome limitations with cellular silicone foams, LLNL innovators have developed a new 3D energy absorbing material with tailored/engineered bulk-scale properties. The energy absorbing material has 3D patterned architectures specially designed for specific energy absorbing properties. The combination of LLNL's capabilities in advanced modeling and simulation and the additive…
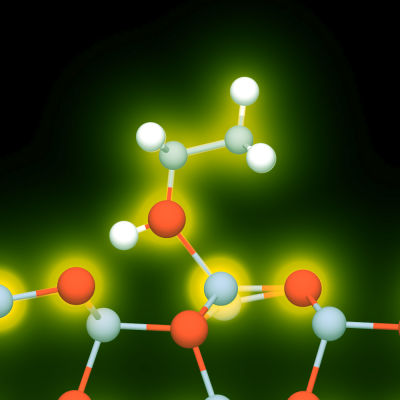
Chemical and biological sensors based on nanowire or nanotube technologies exhibit observable ultrasensitive detection limits due to their unusually large surface-to-volume architecture. This suggests that nanosensors can provide a distinct advantage over conventional designs. This advantage is further enhanced when the nanosensor can harvest its meager power requirements from the surrounding…
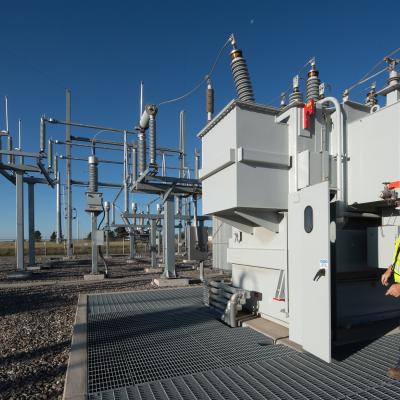
An invention at LLNL uses a mixture of solid and liquid dielectric media. This combination has properties that are an improvement over either separately. The solid phase, in the form of small pellets, inhibits fluid motion, which reduces leakage currents, while the liquid phase (dielectric oil) provides self-repair capabilities. Also, since the media is removable, the high voltage equipment…
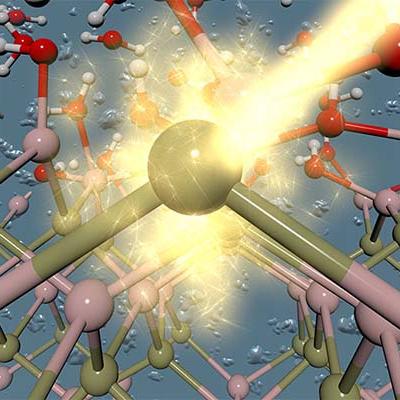
Dubbed the "LLNL Chemical Prism", the LLNL system has use wherever there is a need to separate components of a fluid. A few examples include:
- Chemical detection for known and previously unknown chemicals or substances
- Separation of biomolecules from a cellular extract
- Fractionation of a complex mixture of hydrocarbons
- Forensic analysis of…

LLNL has developed novel nanoporous carbon materials for the surface-stress-induced actuator technology. The morphology of these materials has been designed to combine high surface area and mechanical strength. The process allows for the fabrication of large monolithic pieces with low densities and high structural integrity. One actuation technology relies on electrochemically- induced changes…