This LLNL invention is comprised of (1) a volumetric subtractive manufacturing system which can tomographically manufacture 3D structures with negative features (materials in negative space is degraded with light exposure), and (2) a hybrid volumetric additive/subtractive manufacturing system in which a gelled/solid structure is printed by resin material polymerization using one light, and…
Keywords
- Show all (45)
- Additive Manufacturing (31)
- Manufacturing Automation (2)
- Manufacturing Improvements (2)
- Additively Manufactured (AM) Optics (1)
- Manufacturing Simulation (1)
- Microfabrication (1)
- Precision Engineering (1)
- Synthesis and Processing (1)
- (-) 3D Printing (3)
- (-) Volumetric Additive Manufacturing (2)
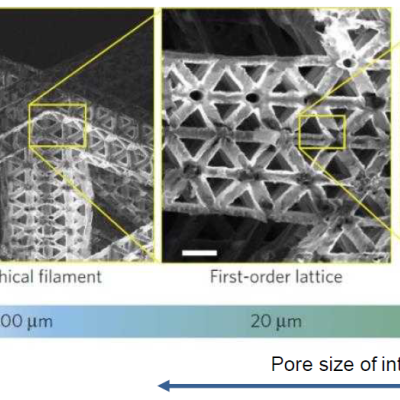
To get the best of both worlds – the sensitivity of LC-MS with the speed of PS-MS – and a functional substrate that can maintain sample integrity, LLNL researchers looked to 3D printing. They have patented a novel approach to create lattice spray substrates for direct ionization mass spectroscopy using 3D-printing processes.

LLNL researchers, through careful control over the chemistry, network formation, and crosslink density of the ink formulations as well as introduction of selected additives, have been successful in preparing 3D printable silicone inks with tunable material properties. For DIW (direct in writing) applications, LLNL has a growing IP portfolio around 3D printable silicone feedstocks for…
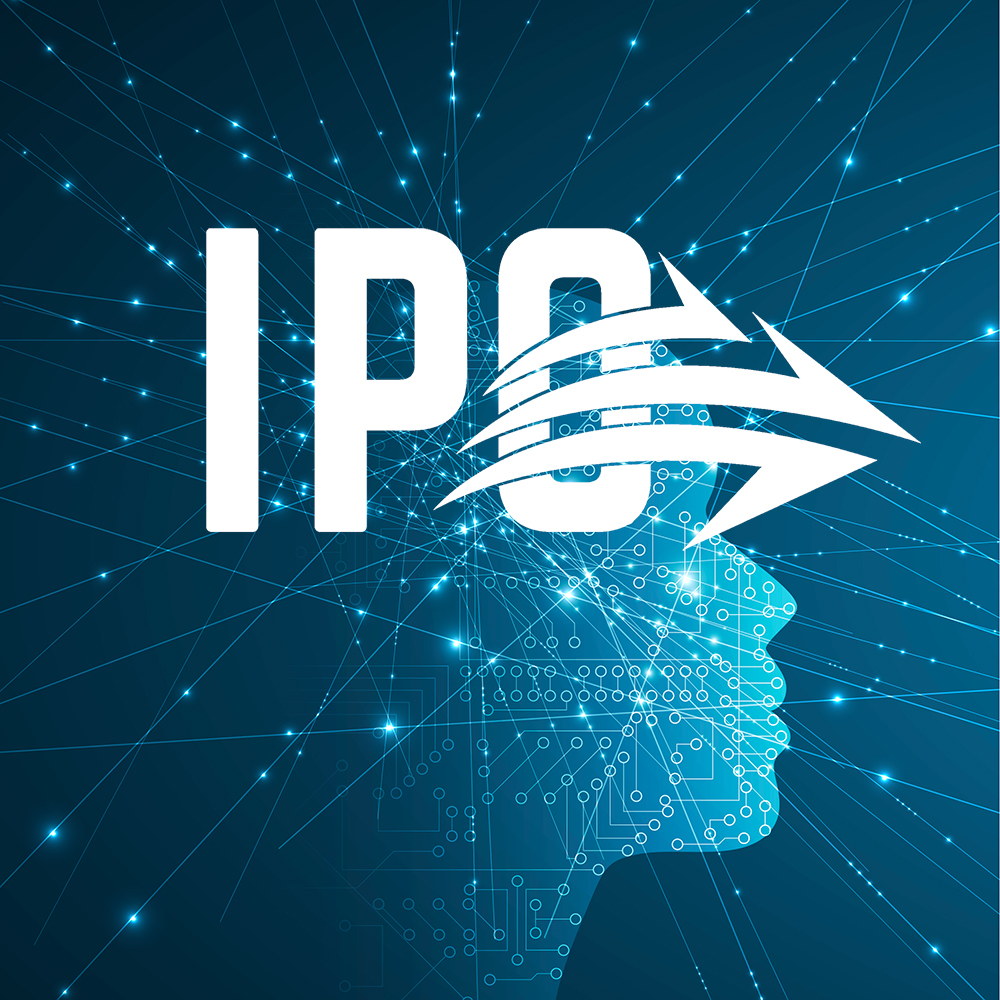
LLNL’s method of 3D printing fiber-reinforced composites has two enabling features:
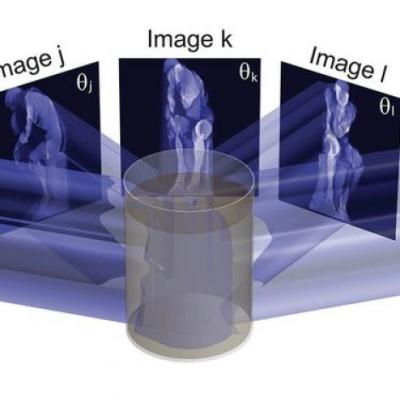
LLNL has developed a system and method that accomplishes volumetric fabrication by applying computed tomography (CT) techniques in reverse, fabricating structures by exposing a photopolymer resin volume from multiple angles, updating the light field at each angle. The necessary light fields are spatially and/or temporally multiplexed, such that their summed energy dose in a target resin volume…