LLNL researchers has developed a composite copper current collector formulation readily used in DIW 3D printing to guide lithium-ion plating/dissolution during charging and discharging cycles.
Keywords
- Show all (239)
- Additive Manufacturing (54)
- Instrumentation (41)
- Synthesis and Processing (21)
- Sensors (14)
- Diagnostics (12)
- Imaging Systems (9)
- Photoconductive Semiconductor Switches (PCSS) (9)
- Electric Grid (7)
- Materials for Energy Products (7)
- Semiconductors (7)
- Substrate Engraved Meta-Surface (SEMS) (7)
- Therapeutics (7)
- Compact Space Telescopes (6)
- Brain Computer Interface (BCI) (5)
- Data Science (5)
- Diode Lasers (5)
- Optical Switches (5)
- (-) 3D Printing (8)
- (-) Carbon Utilization (6)
- (-) Laser Materials Processing (4)
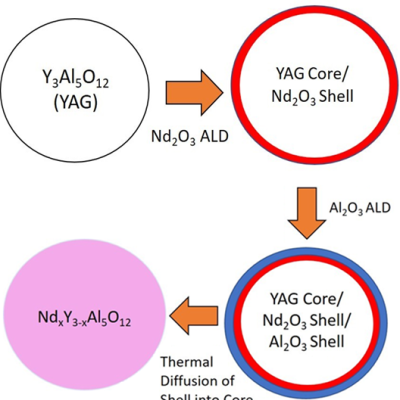
Powder atomic layer deposition process is used to coat nanopowders of host materials (e.g. yttrium aluminum garnet) with optically active neodymium organometal precursor followed by O2/O3 RF plasma to convert to a single layer of Nd2O3. The process can be repeated to build arbitrarily thick layers with custom doping profiles and followed by post-…
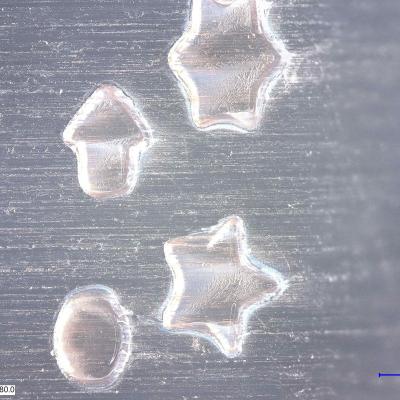
LLNL’s invention is a photopolymerizable polymer resin that consists of one or more nitrile-functional based polymers. The resin is formulated for SLA based 3D printing allowing for the production of nitrile-containing polymer components that can then be thermally processed into a conductive, highly graphitic materials. The novelty of the invention lies in (1) the photo-curable nitrile-…

LLNL’s researchers use physical vapor deposition (sputter deposition or electron beam deposition) to coat an inert gasket material (i.e. PTFE) with a conductive metal (i.e. copper). The gas diffusion electrode overlaps onto the copper coated gasket to allow for electrical conductivity between the catalyst surface and the flow field/current collector of a CO2 electrolyzer. The coated gasket…
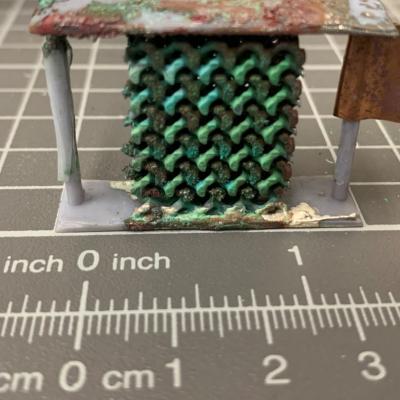
LLNL researchers have developed a fabrication process for creating 3D random interdigitated architectures of anodes and cathodes, eliminating the need for a membrane to separate them. This approach is similar to the repeating interdigitated multi-electrode architectures that also were developed at LLNL.
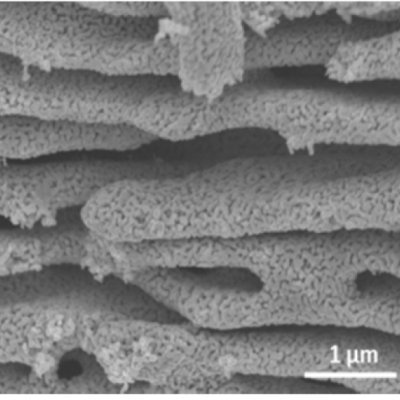
Using their computational design optimization, LLNL researchers have developed copper-based dilute alloy catalysts (contains <10 at.% of the minority metal alloy component) and demonstrated these novel catalysts have improved energy efficiency and selectivity of the methane conversion reaction. By alloying copper with a small amount of the electropositive minority metal element, the…
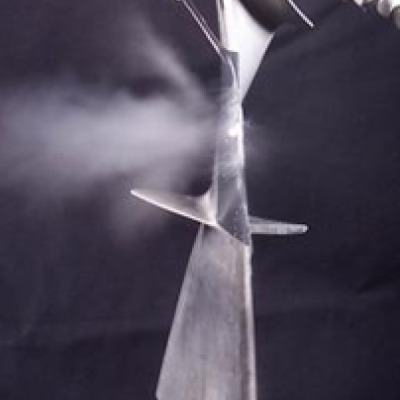
This invention proposes using a pulse laser configured to generate laser pulses and a controller for controlling operation of the pulse laser. The controller is further configured to control the pulse laser to cause the pulse laser to generate at least one of the laser pulses with a spatiotemporally varying laser fluence over a duration of at least one of the laser pulses. The spatiotemporally…
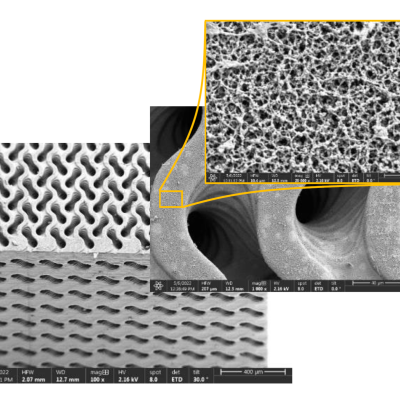
LLNL researchers have developed novel advanced manufactured biomimetic 3D-TPMS (triply periodic minimal surface) membrane architectures such as a 3D gyroid membrane. The membrane is printed using LLNL's nano-porous photoresist technology. LLNL’s 3D-TPMS membranes consist of two independent but interpenetrating macropore flow channel systems that are separated by a thin nano-porous wall…
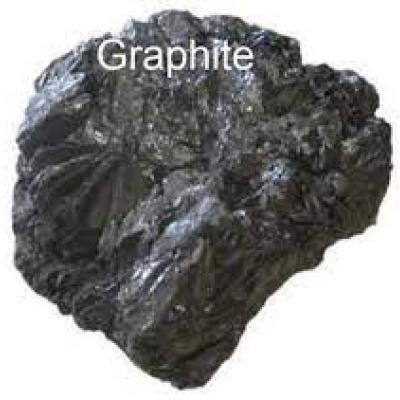
LLNL’s innovation offers an alternate synthetic route to graphite at lower cost using a molten salt mixture of CaCl2-CaCO3-CaO. The synthetic production of graphite and other high-value carbon materials is accomplished in molten salt media via electrochemical reduction and transformation of the carbon from the carbonate ion. The broad electrochemical window of molten salts enables the…
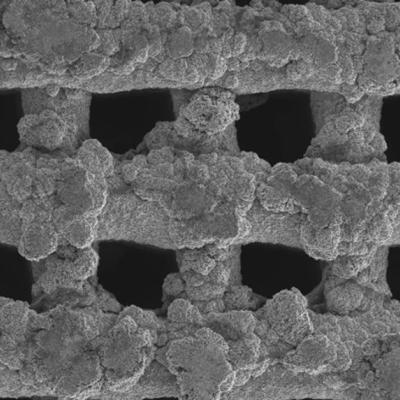
Improving the active material of the Zn anode is critical to improving the practicality of Zn-MnO2 battery technology. LLNL researchers have developed a new category of 3D structured Zn anode using a direct-ink writing (DIW) printing process to create innovative hierarchical architectures. The DIW ink, which is a gel-based mixture composed of zinc metal powder and organic binders, is…
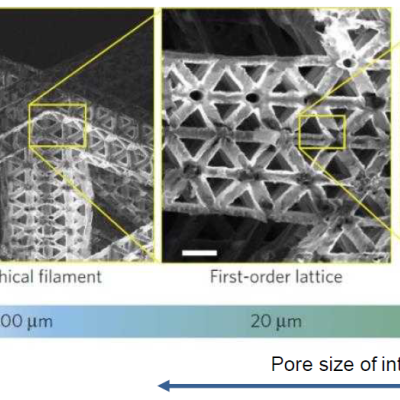
To get the best of both worlds – the sensitivity of LC-MS with the speed of PS-MS – and a functional substrate that can maintain sample integrity, LLNL researchers looked to 3D printing. They have patented a novel approach to create lattice spray substrates for direct ionization mass spectroscopy using 3D-printing processes.

LLNL researchers, through careful control over the chemistry, network formation, and crosslink density of the ink formulations as well as introduction of selected additives, have been successful in preparing 3D printable silicone inks with tunable material properties. For DIW (direct in writing) applications, LLNL has a growing IP portfolio around 3D printable silicone feedstocks for…
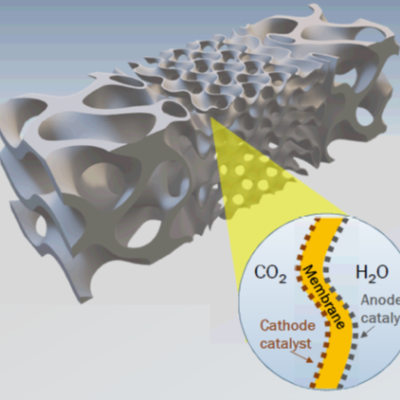
The novel LLNL approach is to use projection microstereolithography (LAPµSL), starting with a photocurable methacrylate resin formulation consisting of a combination of a photoinitiator, photoabsorber, inhibitor, solvents, and other additives. Prior to use, the resin is pretreated to control viscosity for easier handling. The resin is fed to a LAPµSL printer which employs a near UV…
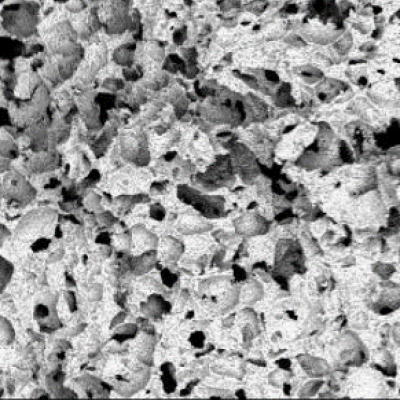
The inventors have developed a 3% Yttria partially-stabilized Zirconia (3YZ) ceramic ink that produces parts with both nano and microporosity and is compatible with two AM techniques: DIW and projection microstereolithography (PμSL). The 3YZ nano-porous ceramic printed parts had engineered macro cavities measuring several millimeters in length, wall thicknesses ranging from 200 to 540 μm, and…
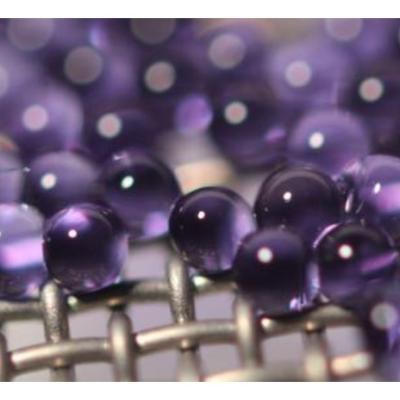
This invention describes a multiple nozzle microfluidic unit that allows simultaneous generation streams of multiple layered coaxial liquid jets. Liquids are pumped into the device at a combined flow rate from 100 mL/hr to 10 L/hr. Droplets are created with diameters in the range of 1 µm to 5 mm and can be created with 1-2 shell layers encapsulating fluid. Droplets created from the system can…
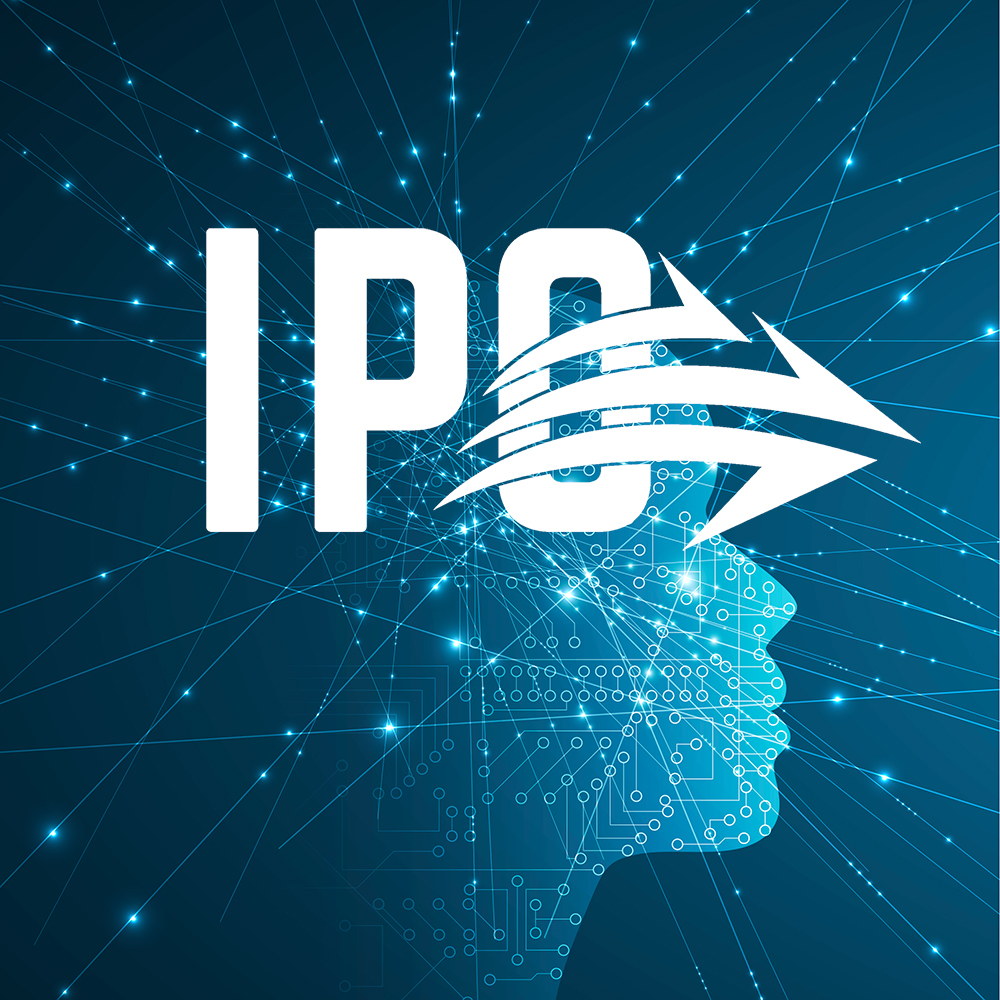
LLNL’s method of 3D printing fiber-reinforced composites has two enabling features:
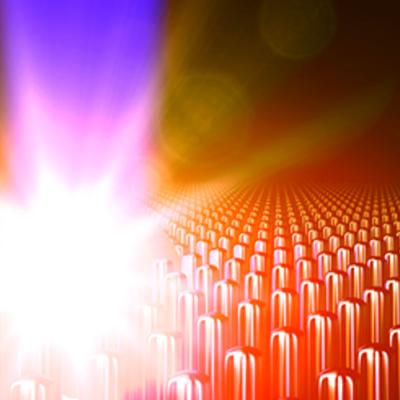
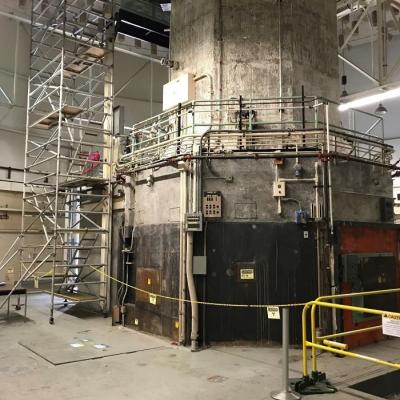
The new LLNL technique works by transiently removing and trapping concrete or rock surface material, so that contaminants are confined in a manner that is easy to isolate and remove. Our studies suggest that 10 m2 of surface could be processed per hour. The technique easily scales to more surface/hr.