LLNL’s researchers use physical vapor deposition (sputter deposition or electron beam deposition) to coat an inert gasket material (i.e. PTFE) with a conductive metal (i.e. copper). The gas diffusion electrode overlaps onto the copper coated gasket to allow for electrical conductivity between the catalyst surface and the flow field/current collector of a CO2 electrolyzer. The coated gasket…
Keywords
- Show all (40)
- Electric Grid (7)
- Additive Manufacturing (4)
- Materials for Energy Products (4)
- 3D Printing (3)
- Direct Air Capture (3)
- Inertial Fusion Energy (IFE) (2)
- Power Electronics (2)
- Geologic Storage (1)
- Inertial Confinement Fusion (ICF) (1)
- Membranes (1)
- Microfabrication (1)
- Photoconductive Semiconductor Switches (PCSS) (1)
- Semiconductors (1)
- Simulation (1)
- (-) Carbon Utilization (6)
- (-) Synthesis and Processing (2)
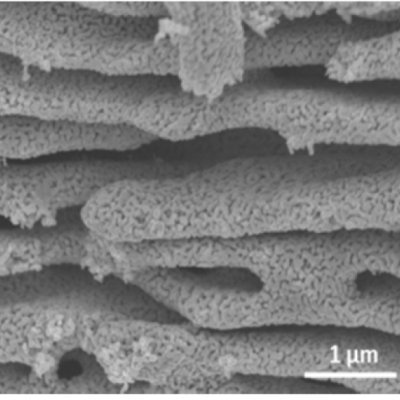
Using their computational design optimization, LLNL researchers have developed copper-based dilute alloy catalysts (contains <10 at.% of the minority metal alloy component) and demonstrated these novel catalysts have improved energy efficiency and selectivity of the methane conversion reaction. By alloying copper with a small amount of the electropositive minority metal element, the…
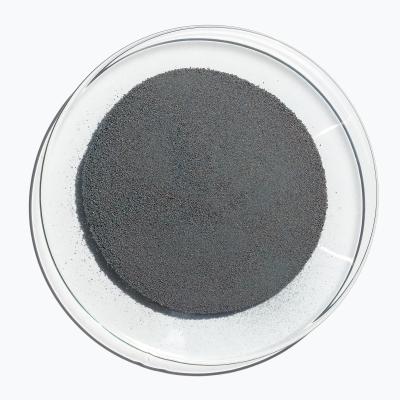
LLNL researchers have developed a Li-Sn-Zn ternary alloy and its method of production. Instead of traditional alloying techniques, the alloy was synthesized using mechanical alloying (high energy ball milling). With high purity elemental powders of lithium, tin and zinc, LLNL researchers were able to prepare Li60Sn20Zn20 as well as Li70Sn20Zn10 nanopowders.
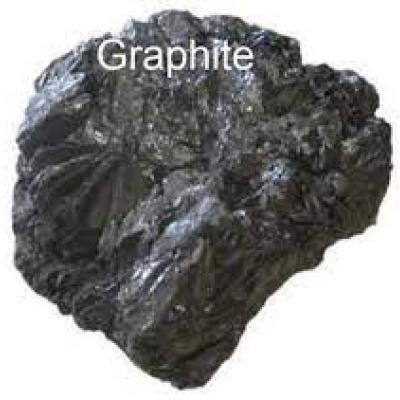
LLNL’s innovation offers an alternate synthetic route to graphite at lower cost using a molten salt mixture of CaCl2-CaCO3-CaO. The synthetic production of graphite and other high-value carbon materials is accomplished in molten salt media via electrochemical reduction and transformation of the carbon from the carbonate ion. The broad electrochemical window of molten salts enables the…
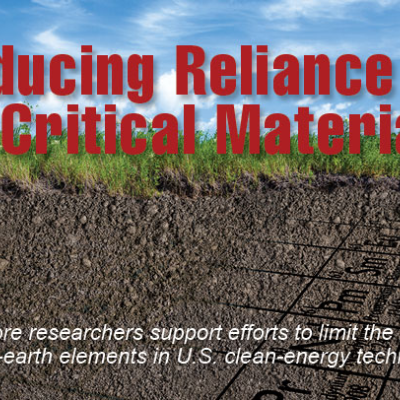
CMI—a DOE Energy Innovation Hub—is a public/private partnership led by the Ames Laboratory that brings together the best and brightest research minds from universities, national laboratories (including LLNL), and the private sector to find innovative technology solutions to make better use of materials critical to the success of clean energy technologies as well as develop resilient and secure…
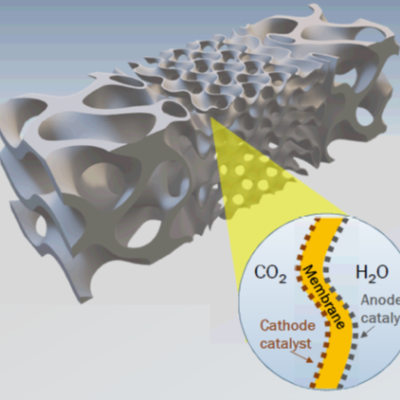
The novel LLNL approach is to use projection microstereolithography (LAPµSL), starting with a photocurable methacrylate resin formulation consisting of a combination of a photoinitiator, photoabsorber, inhibitor, solvents, and other additives. Prior to use, the resin is pretreated to control viscosity for easier handling. The resin is fed to a LAPµSL printer which employs a near UV…
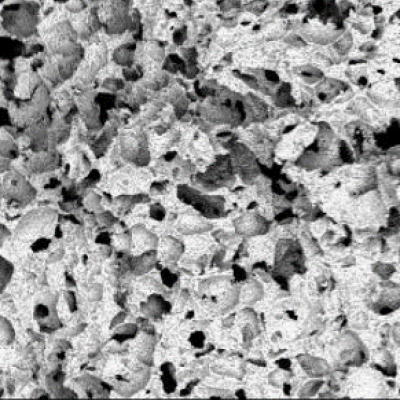
The inventors have developed a 3% Yttria partially-stabilized Zirconia (3YZ) ceramic ink that produces parts with both nano and microporosity and is compatible with two AM techniques: DIW and projection microstereolithography (PμSL). The 3YZ nano-porous ceramic printed parts had engineered macro cavities measuring several millimeters in length, wall thicknesses ranging from 200 to 540 μm, and…
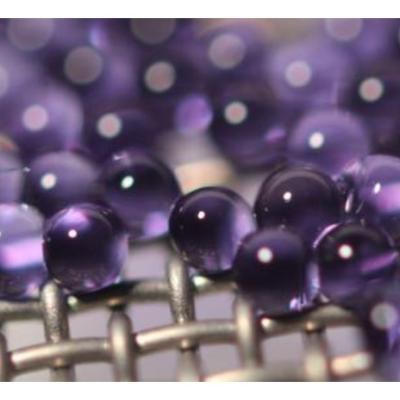
This invention describes a multiple nozzle microfluidic unit that allows simultaneous generation streams of multiple layered coaxial liquid jets. Liquids are pumped into the device at a combined flow rate from 100 mL/hr to 10 L/hr. Droplets are created with diameters in the range of 1 µm to 5 mm and can be created with 1-2 shell layers encapsulating fluid. Droplets created from the system can…