Powder atomic layer deposition process is used to coat nanopowders of host materials (e.g. yttrium aluminum garnet) with optically active neodymium organometal precursor followed by O2/O3 RF plasma to convert to a single layer of Nd2O3. The process can be repeated to build arbitrarily thick layers with custom doping profiles and followed by post-…
Keywords
- Show all (73)
- Photoconductive Semiconductor Switches (PCSS) (9)
- Imaging Systems (8)
- Semiconductors (6)
- Compact Space Telescopes (5)
- Diode Lasers (4)
- Optical Switches (4)
- Sensors (4)
- Power Electronics (3)
- Precision Optical Finishing (3)
- RF Photonics (3)
- Computing (2)
- Electric Grid (2)
- MEMS Sensors (2)
- Optical Sensors (2)
- Precision Engineering (2)
- Spectrometers (2)
- Ultrashort Pulse Lasers (2)
- (-) Laser Materials Processing (5)
- (-) Optical Damage Mitigation (3)
- (-) Particle Accelerators (2)
Technology Portfolios
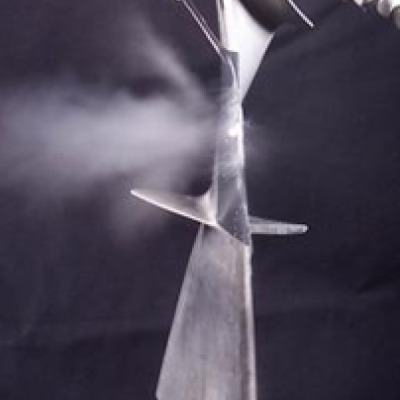
This invention proposes using a pulse laser configured to generate laser pulses and a controller for controlling operation of the pulse laser. The controller is further configured to control the pulse laser to cause the pulse laser to generate at least one of the laser pulses with a spatiotemporally varying laser fluence over a duration of at least one of the laser pulses. The spatiotemporally…
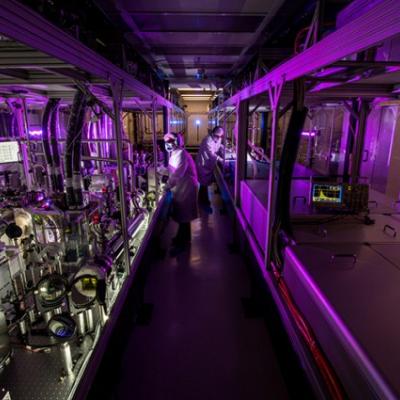
LLNL researchers have developed a high average power Faraday rotator that is gas-cooled and uniquely designed to dissipate heat uniformly so that it does not build up in the optical component and affect its performance. The Faraday rotator material is sliced into smaller disks like a loaf of bread so that high speed helium gas can flow between the slices. With this highly efficient cooling…
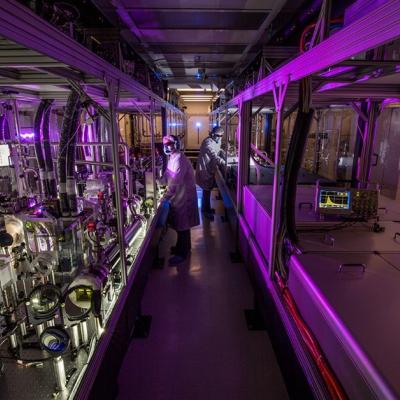
This invention discloses a method to minimize transient variations in the wavelength- and/or pointing-behavior of an optic, without requiring a reduction in its thermal resistance, optical absorption, or operating irradiance. The invention employs a combination of a time-varying heat source and time-varying thermal resistance and/or heat sink temperature to achieve temperature stability of the…
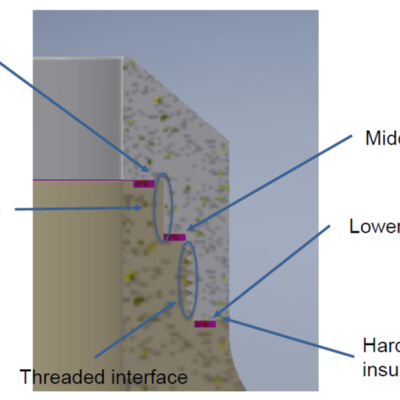
The approach is to build a high voltage insulator consisting of two materials: Poly-Ether-Ether-Ketone (“PEEK”) and Machinable Ceramic (“MACOR”). PEEK has a high stress tolerance but cannot withstand high temperatures, while MACOR has high heat tolerance but is difficult to machine and can be brittle. MACOR is used for the plasma-facing surface, while PEEK will handle the stresses and high…
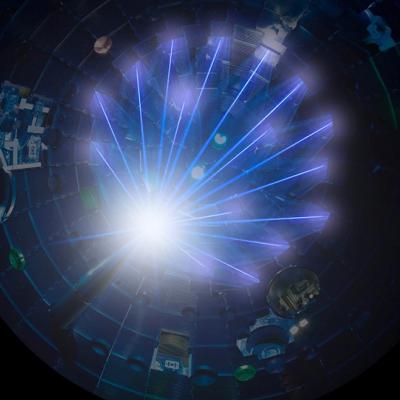
This invention concerns a new type of optic: a transient gas or plasma volume grating produced indirectly by small secondary lasers or directly by nonlinear processes using the primary beams themselves. When used in conjunction with advantageously placed shielding it offers a means of protecting the final optical components of a high-repetition-rate IFE facility. These transmission optics are…
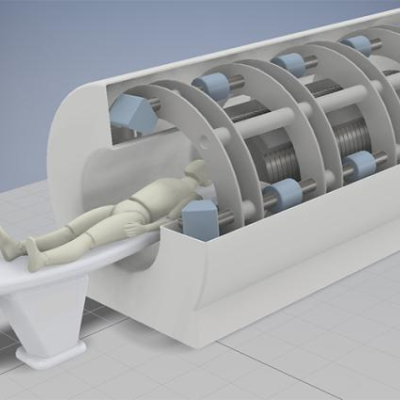
LLNL’s approach is to use their patented Photoconductive Charge Trapping Apparatus (U.S. Patent No. 11,366,401) as the active switch needed to discharge voltage across a vacuum gap in a particle accelerator, like the one described in their other patent (U.S. Patent No.
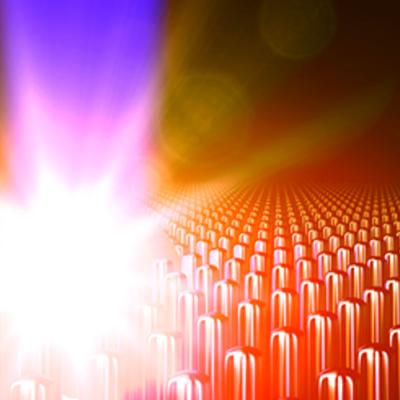
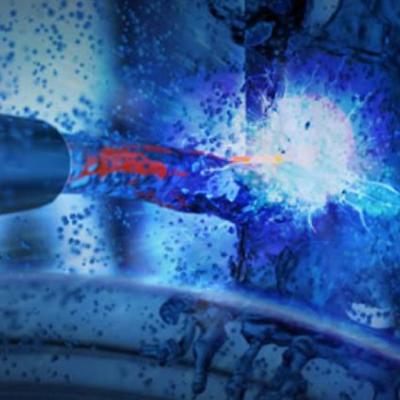
LLNL’s system consists of one or more flashlamp-pumped Nd:glass zig-zag amplifiers, a very low threshold stimulated-Brillouin-scattering (SBS) phase conjugator system, and a free-running single frequency Nd:YLF master oscillator.
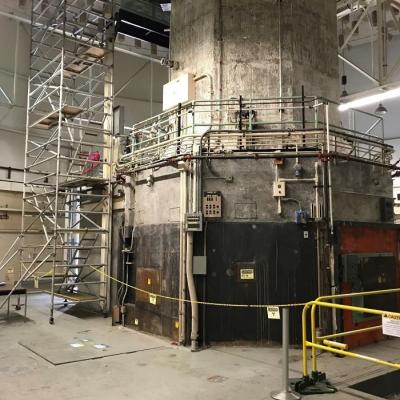
The new LLNL technique works by transiently removing and trapping concrete or rock surface material, so that contaminants are confined in a manner that is easy to isolate and remove. Our studies suggest that 10 m2 of surface could be processed per hour. The technique easily scales to more surface/hr.