LLNL inventors have developed a new multi-wavelength laser scanning system for use in two-photon printing. By integrating multiple laser beams with various choices of wavelengths, the invention provides a new pathway to fabricating a multi-material 3D structure in a single vat process while achieving increased printing resolution beyond diffraction limit. The technology uses multiple…
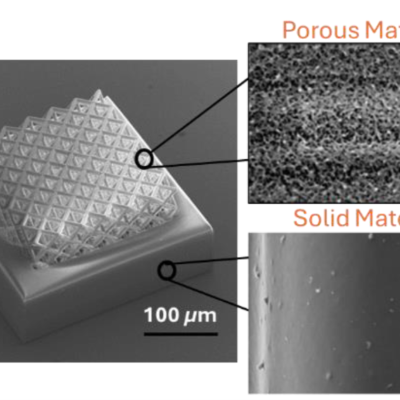
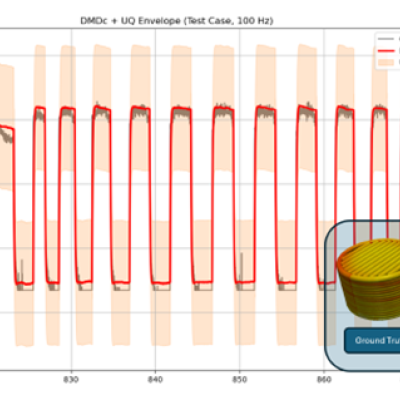
This invention addresses the critical challenge of achieving consistent results in additive manufacturing by introducing a novel system that integrates a comprehensive array of sensors into the manufacturing process. These sensors gather multiple data streams, which are then used to construct a detailed model of the system. The key innovation is its ability to handle MIMO while maintaining…
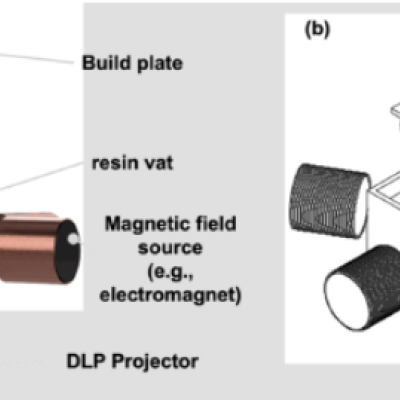
This LLNL invention is capable of generating, on-the-fly, tunable magnetic field strengths with voxel-by-voxel alignment. The approach is to use a custom designed Halbach array consisting of permanent magnets or electromagnets to provide a uniform magnetic field in any direction. This Halbach array will then be coupled with a stereolithography (SLA) printer so that locally aligned…
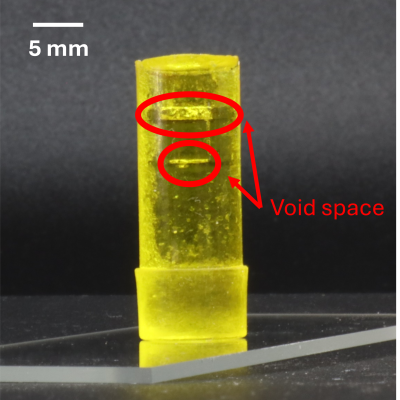
This LLNL invention is comprised of (1) a volumetric subtractive manufacturing system which can tomographically manufacture 3D structures with negative features (materials in negative space is degraded with light exposure), and (2) a hybrid volumetric additive/subtractive manufacturing system in which a gelled/solid structure is printed by resin material polymerization using one light, and…
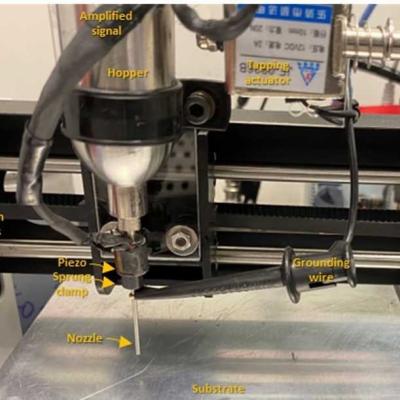
LLNL researchers have developed a piezo-driven jetting powder AM method that provides better control of the packing of printed powder. Powder is fed via a stainless-steel hopper to a nozzle; at the narrowest necking point the powder jams, and flow ceases. A vibrating piezoelectric element (with through-thickness vibration mode) is driven by a 150V AC signal to disturb the jammed powder,…
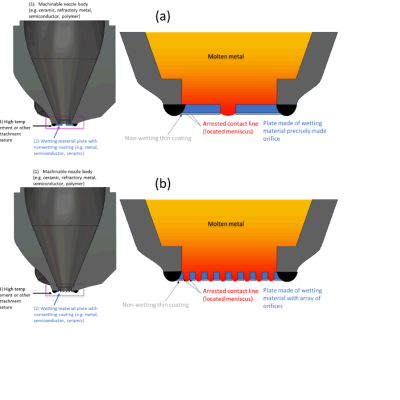
Nozzle design and manufacturing greatly affects the performance of LMJ printers. This LLNL invention describes a novel multi-part nozzle design that improves their performance.
The approach that LLNL researchers developed involve:
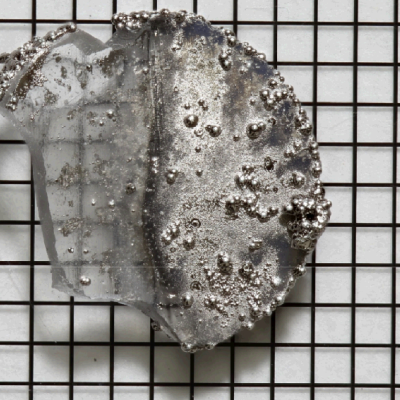
LLNL researchers have continued to develop their pioneering DIW 3D-printed glass optics technology that allows for the 3D printing of single- and multi-material optical glass compositions in complex shapes. This LLNL invention further proposes incorporating dopants (including, but not limited to TiO2 and Pd) into slurries and inks for 3D printing of glass components that can then be directly…
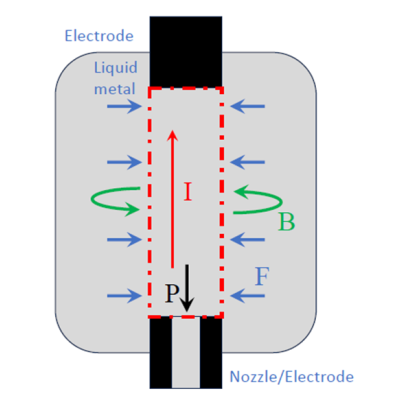
LLNL researchers developed an approach that uses a Z-pinch magnetohydrodynamic (“ZMHD”) pulse as the pressure pulse to emit the liquid metal droplets. ZMHD produces a large current pulse to traverse a column of conducting liquid metal. This pulse induces a magnetic field through Ampere’s law, and that field then interacts with the current pulse via the Lorentz force to generate a…
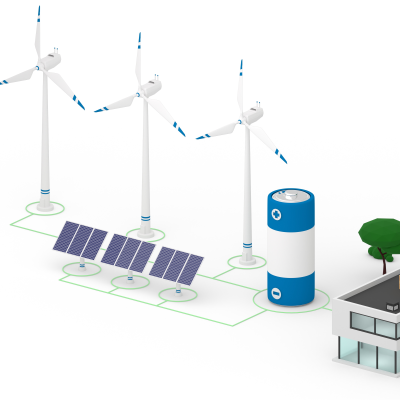
LLNL researchers have designed and produced, both conductive and non-conductive porous electrode components manufactured for improved metal deposition, discharging, and fluid dynamics in hybrid flow batteries. This is achieved through Direct Ink Writing (DIW) additive manufacturing. The engineered 3D electrodes enable uniform current distribution and even metal deposition during…
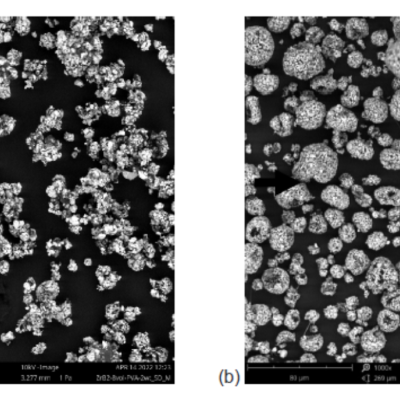
LLNL researchers refined custom mixing techniques and formulations in order to avoid clumping and fiber agglomerations for a flowable tailored feedstock that produces a homogeneous, survivable thermal barrier coating. Formulation improvements coupled with unexpected nozzle coupling from Buchi spray dry components leads to the production of fiber containing spray dried feedstock that can…
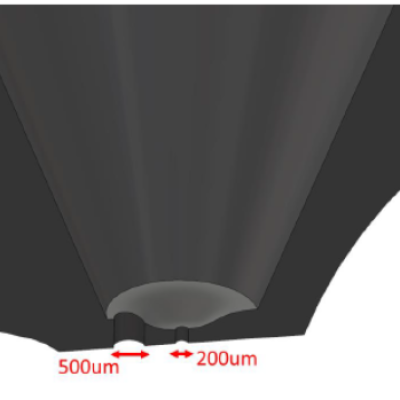
LLNL’s invention combines four approaches to enable on-the-fly multi-resolution metal droplet printing: (1) a nozzle with two or more orifices of varying diameter and length, (2) a set of corresponding pressure pulses that can eject droplets out of some, but not all, orifices in either magnetohydrodynamic (MHD-LMJ) or Pneumatic-LMJ, (3) the ability to change the pressure pulse on demand…
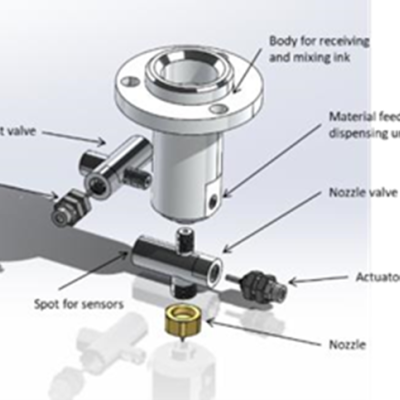
LLNL researchers’ approach to this challenge is to design a modular valve subsystem that redirects the flow away from the main nozzle to an “exhaust”. By re-routing the flow to a different exit port, steady state flow can be better maintained. The re-routing requires actuators that work in tandem; open and close of the nozzle and exhaust valves have to be executed simultaneously. …
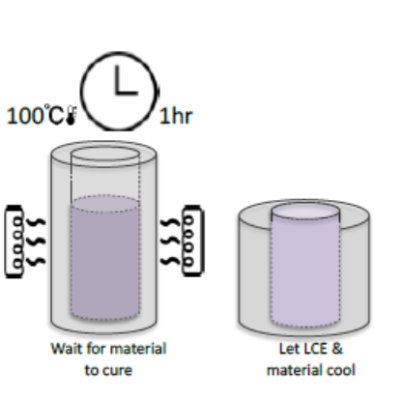
LLNL researchers developed novel workflows where material is first cast into the LCE molds at room temperature. Upon curing, the mold is induced to expand or contract (change shape) by external stimuli (light, heat, solvent) to self-release. A reduction to practice example used silica-loaded silicone ink casted into a LCE cylinder mold. It was cured at 100°C, and self-…
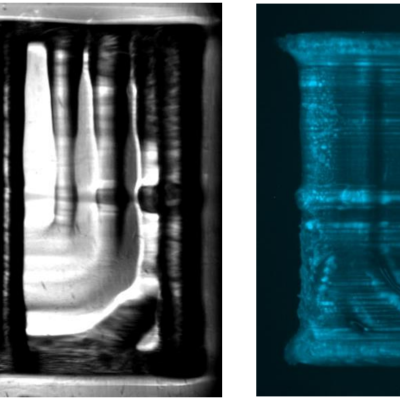
Three important aspects of this invention are: (1) the formulation of a photocurable resin containing a fluorophore that exhibits AIE behavior; (2) the method of in-situ and real-time characterization for monitoring the reaction kinetics during the photopolymerization and UV-curing process; and (3) the application of a new 3D steganographic ink for 3D encrypted structure.
Image Caption:…
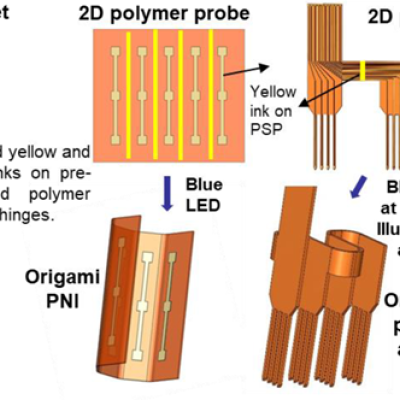
The approach involves 3D printing hinges made of Pre-Stressed Polymers (“PSP”) onto polyimide (“PI”) substrates. These hinges are then able to fold in response to externally applied stimuli, such as light. First, 2D PI devices will be microfabricated. Then, PSP infused with colored inks will be printed using Direct Ink Write (“DIW”) on the hinges of the PI devices. When…
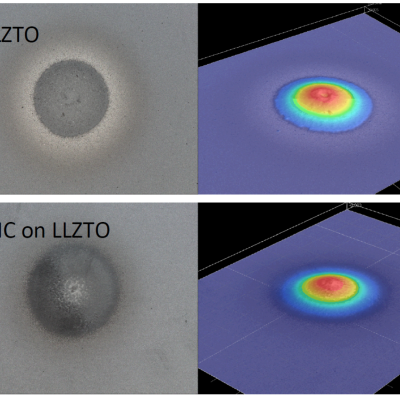
LLNL has co-developed a number of technologies thatuse cold spray deposition that enable new designs for functional materials with low waste.

The novel approach is to make Ultem® into an ink for DIW or droplet printing by dissolving Ultem® in solvents, such as tetrahydrofuran. This produces a viscous solvent-melt that is loaded into an ambient temperature extrusion system and deposited into a defined structure by the 3D printer. Solvent mobility is limited by the polymer structure, and further solvent removal allows…
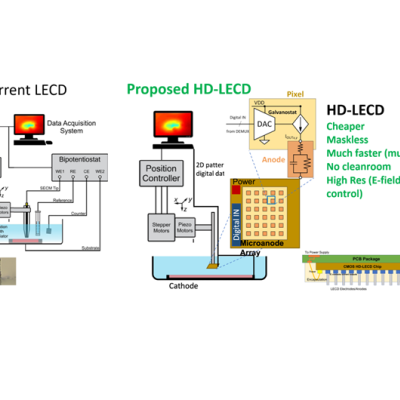
LLNL’s approach is to design and fabricate a massively-parallel microanode printhead using a custom complementary metal-oxide semiconductor integrated circuit (CMOS IC) chip with independent electronics for each pixel. This microanode in close proximity to the cathode surface will electroplate dissolved ions into a small voxel. The probe then moves and continues to deposit material…

LLNL researchers have developed an approach is to use pneumatic droplet ejection devices to rapidly 3D print solid metal parts that also have a smoother surface finish than conventional liquid metal printing. Pneumatic droplet ejection printers can be used in two different modes: “droplet mode” uses pulsed gas pressure to create individual droplets of liquid metal that are collected to…
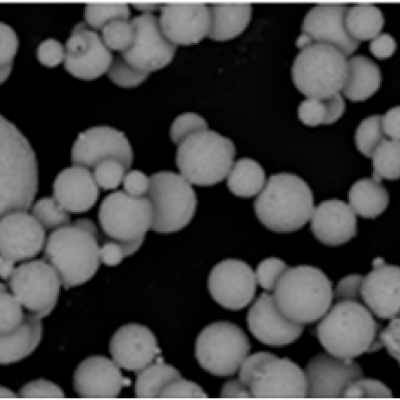
LLNL has developed a process to partially sinter starting material composed of smaller-sized powder particles to obtain a loose powder product that have larger-sized particles. To avoid the undesired formation of a single fully-sintered piece, the starting powder material is heated for a relatively shorter time. The time and temperature required for partial sintering is…
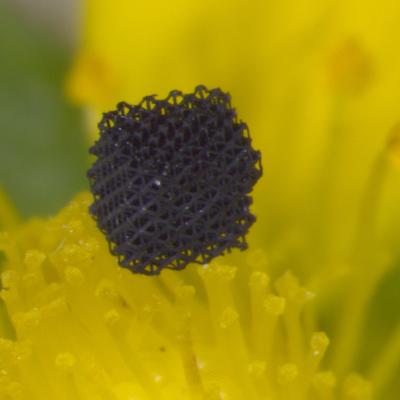
To overcome challenges that existing techniques for creating 3DGs face, LLNL researchers have developed a method that uses a light-based 3D printing process to rapidly create 3DG lattices of essentially any desired structure with graphene strut microstructure having pore sizes on the order of 10 nm. This flexible technique enables printing 3D micro-architected graphene objects with complex,…
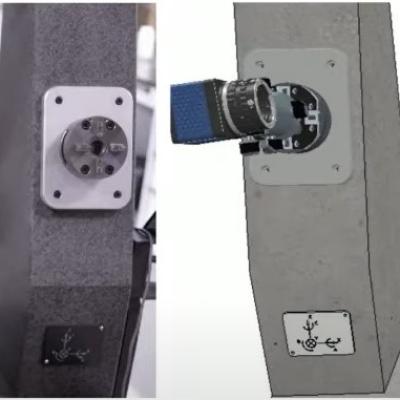
LLNL’s novel approach utilizes a number of techniques to improve reconstruction accuracy:
- Better coding scheme-based techniques
- Hardware-assisted techniques
- Adaptive fringe projection techniques
- Multi-exposure based techniques
The method requires specific calibration procedures and control of the hardware, which is achieved through a digital twin…
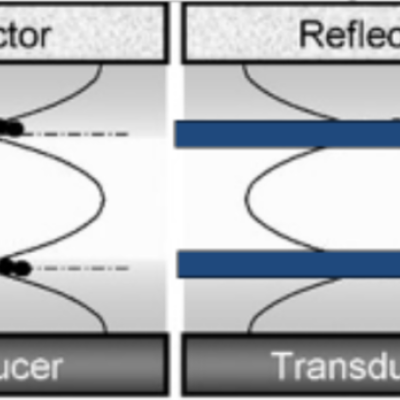
This novel AM approach utilizes cavitation bubbles generated within liquid resin by ultrasonic energy that trigger, induce, or catalyze a polymerization process (3D Ultrasound Polymerization). Ultrasound may be generated by piezoelectric transducers or high-power lasers and by modulating the ultrasound wave (frequency and amplitude), the cavitation site could be directed.

LLNL’s MVAM method comprises of a microwave applicator array coupled to a time-reversal beam steering algorithm to focus and deposit microwave energy in the feedstock material. The selective focusing of high-power microwave fields results in delivery of localized energy to arbitrary regions in a 3D volume. The localized area in the 3D volume heats up, allowing for the curing,…
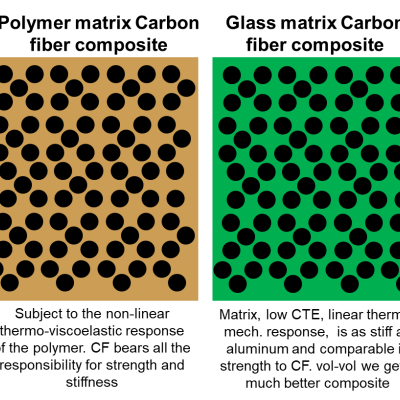
The approach is to combine the techniques of 3D printing aligned carbon fiber composites and melt-3D printing of glasses in a non-obvious manner to allow 3D printing (with controlled microstructure, fiber alignment, complex geometries, and advanced second order composite properties) of a new class of additively manufactured fiber-glass composites. It involves four major elements: …
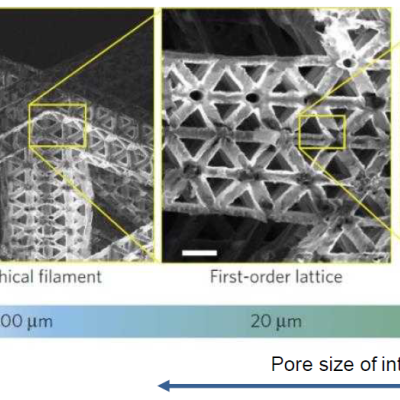
To get the best of both worlds – the sensitivity of LC-MS with the speed of PS-MS – and a functional substrate that can maintain sample integrity, LLNL researchers looked to 3D printing. They have patented a novel approach to create lattice spray substrates for direct ionization mass spectroscopy using 3D-printing processes.

LLNL researchers, through careful control over the chemistry, network formation, and crosslink density of the ink formulations as well as introduction of selected additives, have been successful in preparing 3D printable silicone inks with tunable material properties. For DIW (direct in writing) applications, LLNL has a growing IP portfolio around 3D printable silicone feedstocks for…
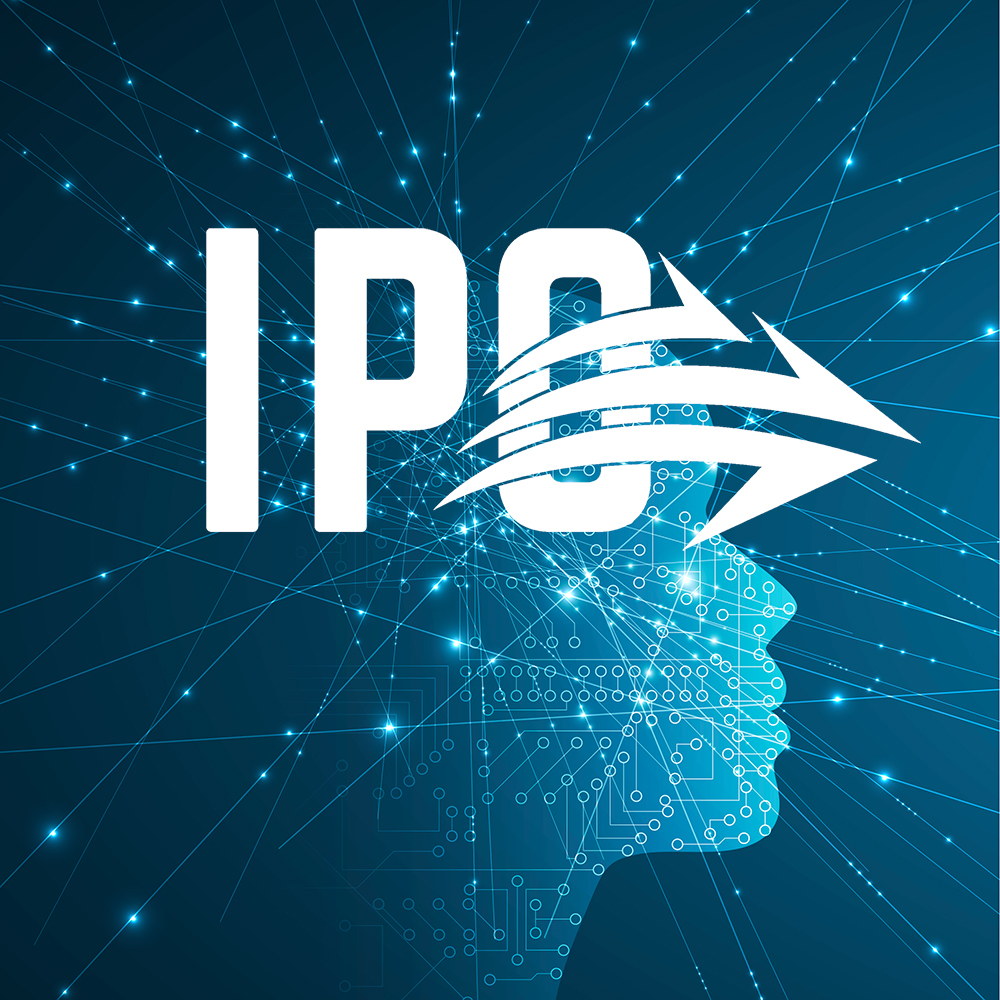
LLNL’s method of 3D printing fiber-reinforced composites has two enabling features:
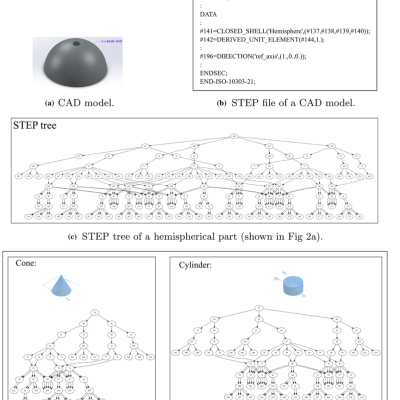
MBD captures the complete specification of a part in digital form and leverages (at least) the universal STEP file format. MBD has revolutionized manufacturing due to time and cost savings associated with containing all engineering data within a single digital source. LLNL researchers have been able to develop a novel encoding method to transform digital definitions in any given STEP file into…
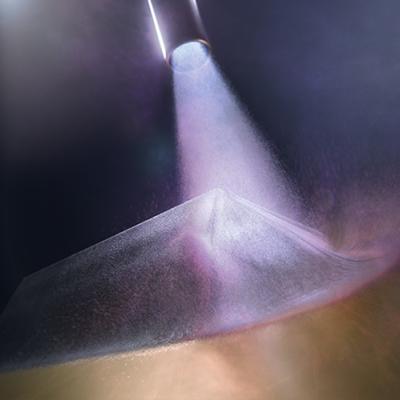
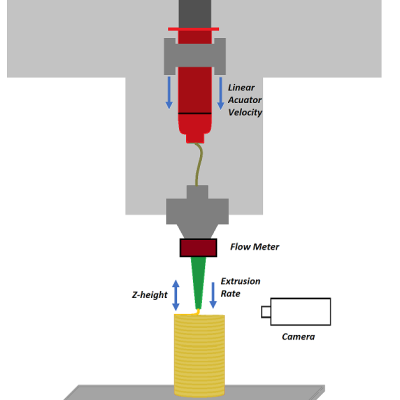
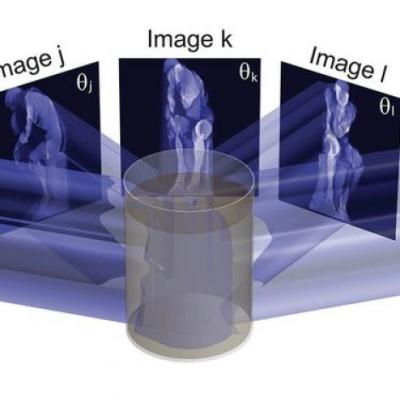
LLNL has developed a system and method that accomplishes volumetric fabrication by applying computed tomography (CT) techniques in reverse, fabricating structures by exposing a photopolymer resin volume from multiple angles, updating the light field at each angle. The necessary light fields are spatially and/or temporally multiplexed, such that their summed energy dose in a target resin volume…
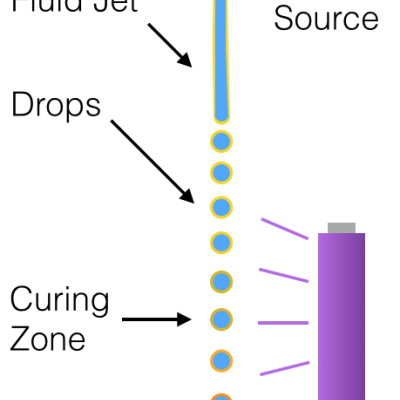
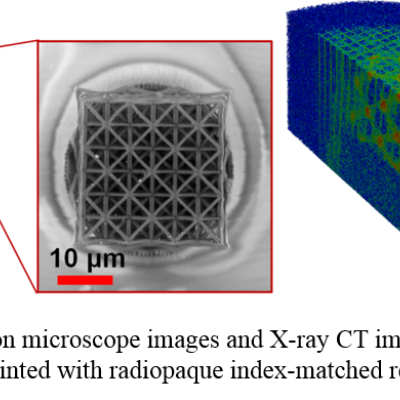
LLNL has developed an optically clear iodine-doped resist that increases the mean atomic number of the part. AM parts fabricated with this resist appear radio-opaque due to an increase in the X-ray attenuation by a factor of 10 to 20 times. Optical clarity is required so that the photons can penetrate the liquid to initiate polymerization and radio opacity is required to enable 3D computed…
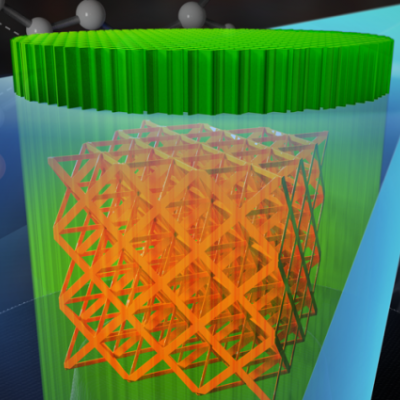
LLNL has solved the challenges of depth-resolved parallel TPL by using a temporal focusing technique in addition to the spatial focusing technique used in serial writing systems. We temporally focus the beam (through optical set-up design) so that a sharp Z-plane can be resolved while projecting 2D “light sheets” that cause localized photo-polymerization. This enables printing of complex 3D…
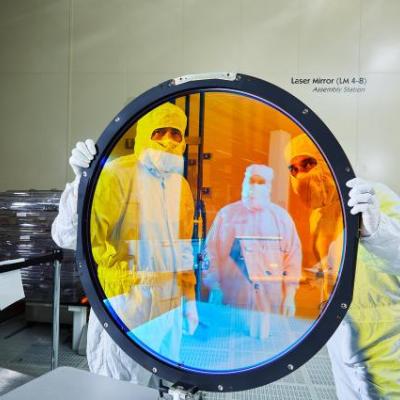
The LLNL method for optimizing as built optical designs uses insights from perturbed optical system theory and reformulates perturbation of optical performance in terms of double Zernikes, which can be calculated analytically rather than by tracing thousands of rays. A new theory of compensation is enabled by the use of double Zernikes which allows the performance degradation of a perturbed…
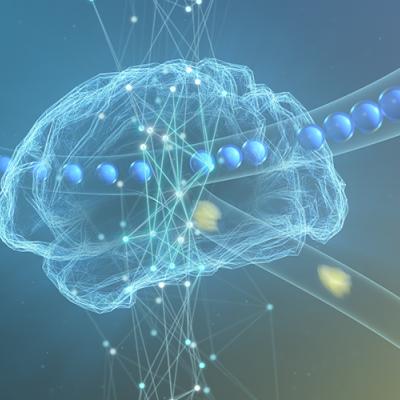
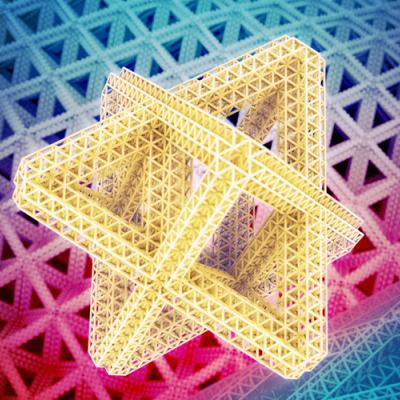