Advanced Manufacturing is the use of innovative technologies to create new or existing products. Lawrence Livermore National Laboratory’s advanced manufacturing portfolio can be organized into four main groups: Additive Manufacturing is the process of joining materials to make objects from 3D model data, usually layer upon layer, as opposed to subtractive manufacturing methodologies. Precision Engineering is the design and fabrication of machines, fixtures, and other structure that have exceptionally low tolerances, are repeatable, and are stable over time. Manufacturing Simulation & Automation comprises technologies that reduce human intervention in manufacturing processes, as well as a set of tools that allows for experimentation and validation of product, process, and system designs & configurations. Manufacturing Improvements are inventions that improve throughput/efficiency, or that reduce cost/waste.
Portfolio News and Multimedia
Seurat Technologies, a Massachusetts-based startup, licensed a LLNL-invented metal AM technology in 2015 with the intention of commercializing a high-speed, high-resolution 3D printer to produce metal parts at industrial scale. Since then, Seurat has developed the lasers, optics, and equipment needed to bring the technology to market, further strengthening LLNL’s mission-driven development of advanced materials and manufacturing processes. In this video, explore how Seurat, with investments from NVIDIA and others, could revolutionize metal additive manufacturing.
In a record setting year for Lawrence Livermore National Laboratory (LLNL), four teams of LLNL researchers will attend the Department of Energy’s (DOE) Energy I-Corps (EIC) Cohort 20 this spring.
The EIC is a key initiative of the DOE’s Office of Technology Commercialization, and facilitated at LLNL by Hannah Farquar from the Innovation and Partnerships Office (IPO). Established in 2015, EIC pairs teams of scientists with industry mentors to train researchers in moving DOE lab-developed technologies toward commercialization.
Through a new process a Lawrence Livermore National Laboratory (LLNL) team is calling Microwave Volumetric Additive Manufacturing (MVAM), researchers have introduced an innovative new approach to 3D printing using microwave energy to cure materials, opening the door to a broader range of materials than ever before.
Check out the technology page for MVAM!
Advanced Manufacturing Technologies
Areas of Focus
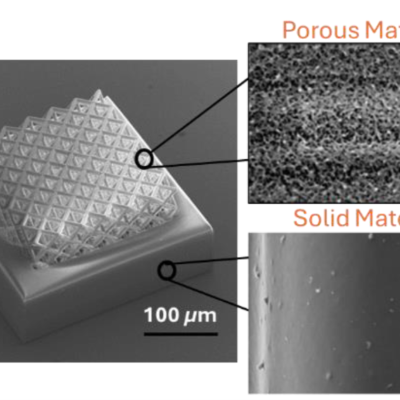
LLNL inventors have developed a new multi-wavelength laser scanning system for use in two-photon printing. By integrating multiple laser beams with various choices of wavelengths, the invention provides a new pathway to fabricating a multi-material 3D structure in a single vat process while achieving increased printing resolution beyond diffraction limit. The technology uses multiple…
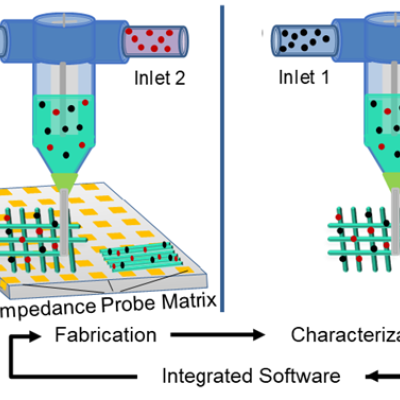
The platform has three major components:
(1) active-mixing direct-ink-write
(2) in situ characterization substrates or probes
(3) active learning experimental planning system.
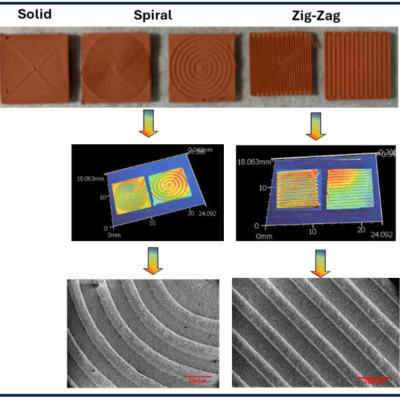
LLNL researchers has developed a composite copper current collector formulation readily used in DIW 3D printing to guide lithium-ion plating/dissolution during charging and discharging cycles.
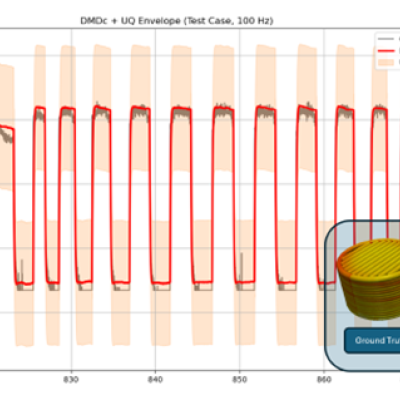
This invention addresses the critical challenge of achieving consistent results in additive manufacturing by introducing a novel system that integrates a comprehensive array of sensors into the manufacturing process. These sensors gather multiple data streams, which are then used to construct a detailed model of the system. The key innovation is its ability to handle MIMO while maintaining…
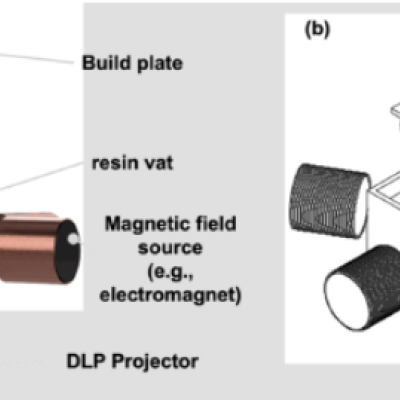
This LLNL invention is capable of generating, on-the-fly, tunable magnetic field strengths with voxel-by-voxel alignment. The approach is to use a custom designed Halbach array consisting of permanent magnets or electromagnets to provide a uniform magnetic field in any direction. This Halbach array will then be coupled with a stereolithography (SLA) printer so that locally aligned…
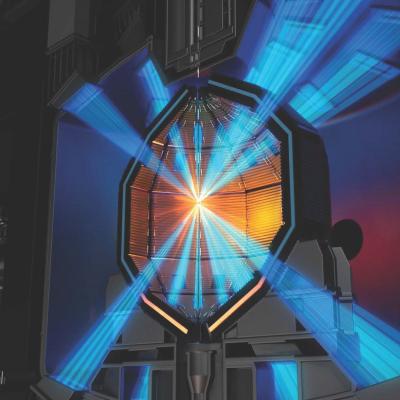
LLNL researchers have developed additive manufactured fuel targets for IFE. They have been successful in using TPL to fabricate low density (down to 60 mg/cm3) and low atomic number (CHO) polymeric foams for potential targets, and some have been tested at the OMEGA Laser Facility. With TPL, LLNL researchers have also been able to fabricate a full fuel capsule with diameter of ~ 5mm or…
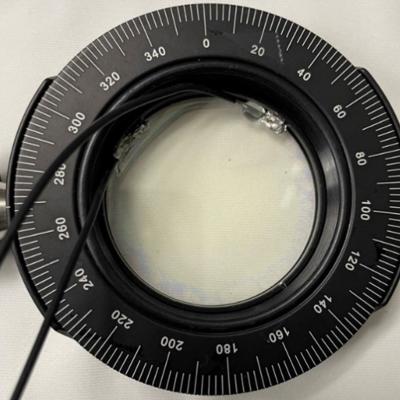
The approach is to use appropriately doped semi-insulating gallium nitride to provide a high damage tolerant photoconductor with high responsivity to various pump wavelength light. Mn, C, or Fe are used as dopants to provide a source of electrons or holes that can be excited. This is combined with the use of dichroic antireflection coating at the GaN/polyimide/liquid crystal…
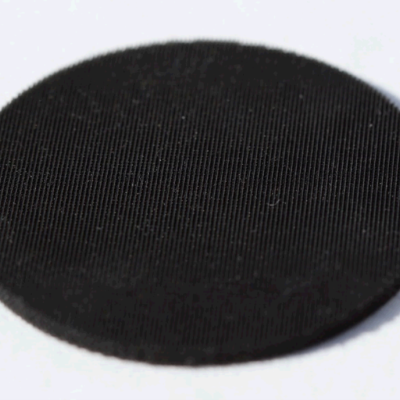
LLNL researchers have developed a silicone based conductive, elastomeric 3D DIW printed structure with a lower wt.% conductive, composite filler to allow for the creation of 3D printed lattice structures with tunable conductivity. The conductivity of the printed structure can be varied using composition of the starting DIW ink formulation as well as the 3D printed spacing and…
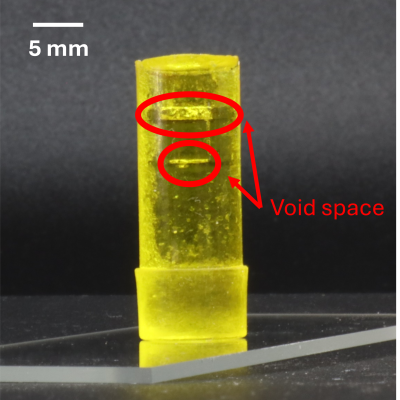
This LLNL invention is comprised of (1) a volumetric subtractive manufacturing system which can tomographically manufacture 3D structures with negative features (materials in negative space is degraded with light exposure), and (2) a hybrid volumetric additive/subtractive manufacturing system in which a gelled/solid structure is printed by resin material polymerization using one light, and…
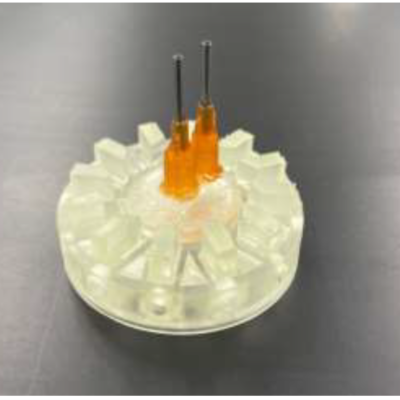
This invention focuses on the design of a fully interchangeable hub-droplet device apparatus for multiple droplet generation in parallel. The novel central hub combined with interchangeable chip configuration allows the use of different planar droplet generation devices that can be replaced and exchanged as needed. By separating the central housing hub which distributes incoming liquids into…
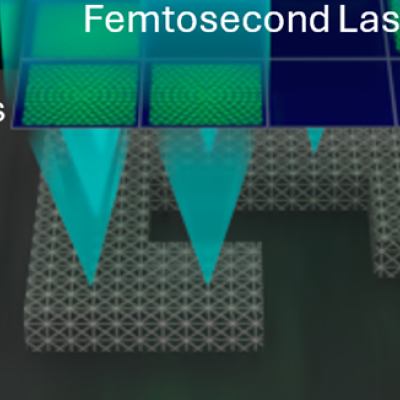
LLNL researchers have developed a parallelized TPP system that combines metalens array and spatial light modulator (SLM) to manipulate the directed laser light, which enables high-volume fabrication of nano-architected structures at wafer-scale. Instead of using a single microscope objective, LLNL’s approach uses an array of metalens that the laser passes through with each metalens being…
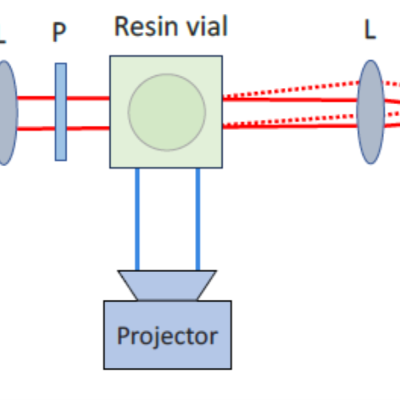
The approach is to use quantitative phase imaging (QPI) using a common-path phase-shifting interferometry technique. A sequence of four phase shifts with an increment of π/2 between unscattered reference beam and scattered sample beam are imparted by a spatial light modulator. A quantitative phase image is retrieved from four raw intensity images. QPI is a highly sensitive…
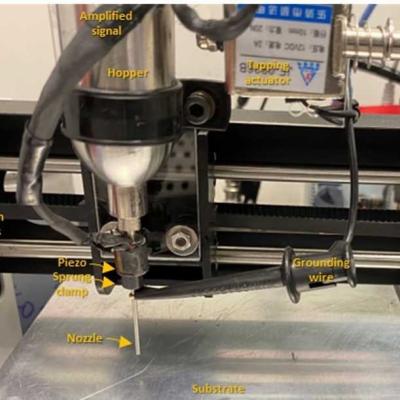
LLNL researchers have developed a piezo-driven jetting powder AM method that provides better control of the packing of printed powder. Powder is fed via a stainless-steel hopper to a nozzle; at the narrowest necking point the powder jams, and flow ceases. A vibrating piezoelectric element (with through-thickness vibration mode) is driven by a 150V AC signal to disturb the jammed powder,…
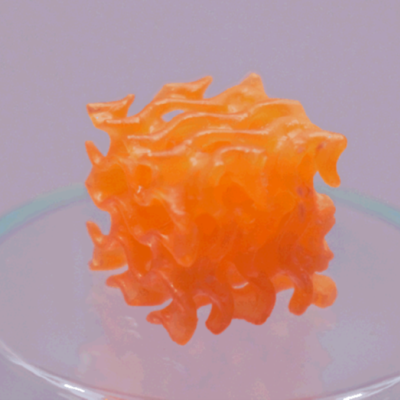
LLNL researchers have developed a method which utilizes functional alcohols to depolymerize polyurethane crosslinked networks. The functional alcohols show 5X increase in the depolymerization efficiency compared with current state of art (e.g. methanol, ethylene glycol). The crosslinked polyurethane networks completely depolymerized into a liquid oligomer within 48 hours at ambient…
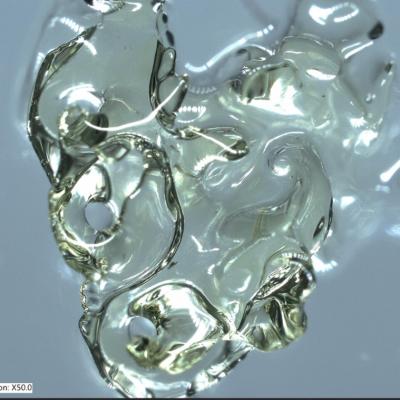
LLNL researchers have developed a novel photocurable silicone useful for producing three-dimensional objects via additive manufacturing. The resin formulations consist of a mult-component siloxane polymers with different functionalities, a platinum catalyst, a photoinitiator, and other organic peroxides. The LLNL invention involves controlling the spatial and temporal aspects of the…
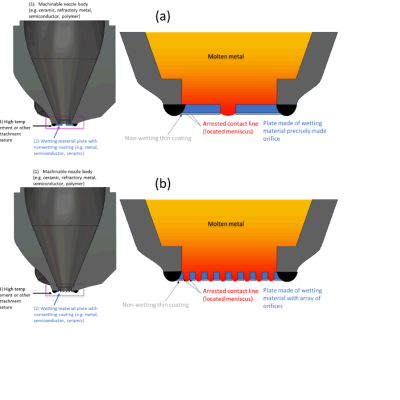
Nozzle design and manufacturing greatly affects the performance of LMJ printers. This LLNL invention describes a novel multi-part nozzle design that improves their performance.
The approach that LLNL researchers developed involve:
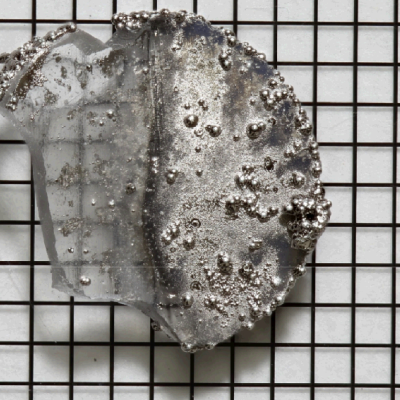
LLNL researchers have continued to develop their pioneering DIW 3D-printed glass optics technology that allows for the 3D printing of single- and multi-material optical glass compositions in complex shapes. This LLNL invention further proposes incorporating dopants (including, but not limited to TiO2 and Pd) into slurries and inks for 3D printing of glass components that can then be directly…
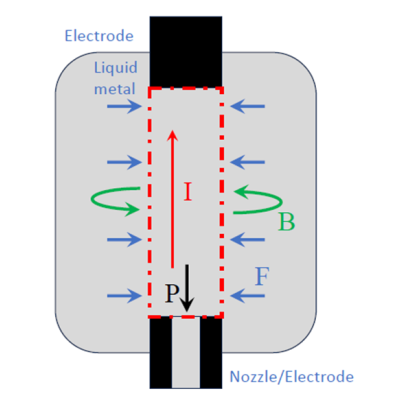
LLNL researchers developed an approach that uses a Z-pinch magnetohydrodynamic (“ZMHD”) pulse as the pressure pulse to emit the liquid metal droplets. ZMHD produces a large current pulse to traverse a column of conducting liquid metal. This pulse induces a magnetic field through Ampere’s law, and that field then interacts with the current pulse via the Lorentz force to generate a…
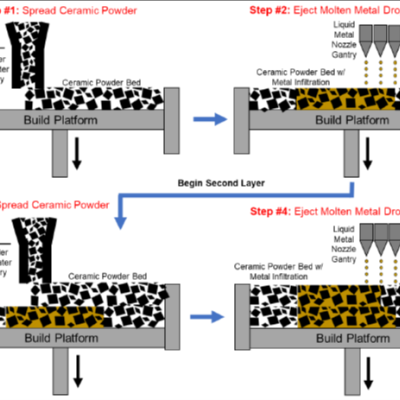
This invention, hereby called liquid metal binder jetting (LMBJ), uses a molten metal as the “binder” that is deposited on ceramic powder, resulting in a multi-material fabrication process that includes both the ceramic and metallic phase in the same process. The simple process involves four steps:
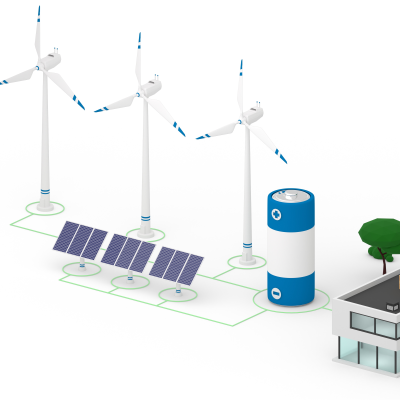
LLNL researchers have designed and produced, both conductive and non-conductive porous electrode components manufactured for improved metal deposition, discharging, and fluid dynamics in hybrid flow batteries. This is achieved through Direct Ink Writing (DIW) additive manufacturing. The engineered 3D electrodes enable uniform current distribution and even metal deposition during…
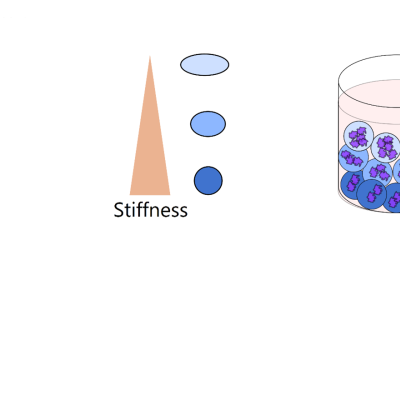
LLNL researchers have enhanced and expanded the IDEA technology, which fabricates micron-scale droplets that are then crosslinked in-air (within milliseconds) using a UV light source before collection. An aerodynamically shearing air jet or acoustic vibration force causes rapid droplet formation.
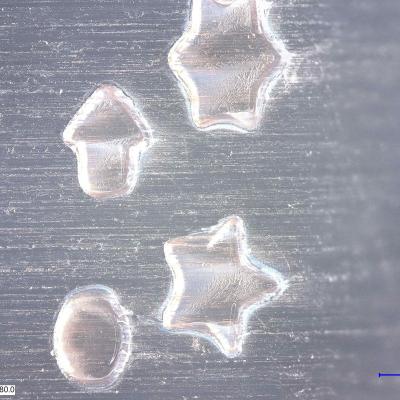
LLNL’s invention is a photopolymerizable polymer resin that consists of one or more nitrile-functional based polymers. The resin is formulated for SLA based 3D printing allowing for the production of nitrile-containing polymer components that can then be thermally processed into a conductive, highly graphitic materials. The novelty of the invention lies in (1) the photo-curable nitrile-…
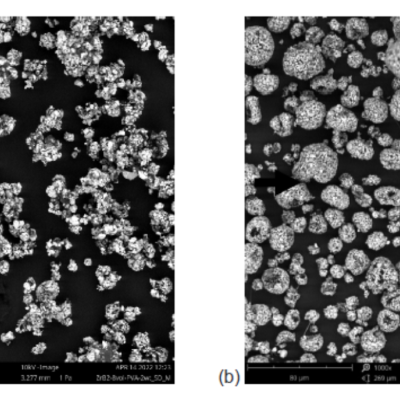
LLNL researchers refined custom mixing techniques and formulations in order to avoid clumping and fiber agglomerations for a flowable tailored feedstock that produces a homogeneous, survivable thermal barrier coating. Formulation improvements coupled with unexpected nozzle coupling from Buchi spray dry components leads to the production of fiber containing spray dried feedstock that can…
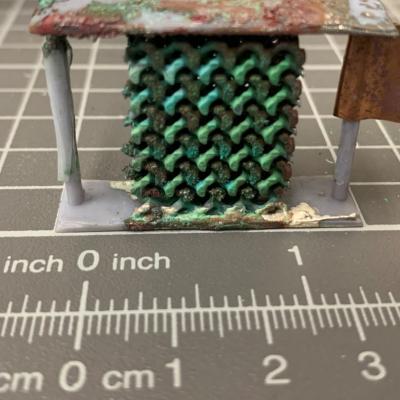
LLNL researchers have developed a fabrication process for creating 3D random interdigitated architectures of anodes and cathodes, eliminating the need for a membrane to separate them. This approach is similar to the repeating interdigitated multi-electrode architectures that also were developed at LLNL.
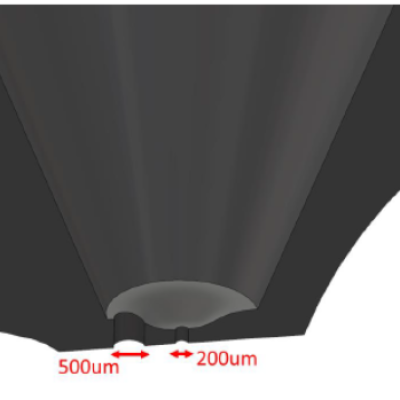
LLNL’s invention combines four approaches to enable on-the-fly multi-resolution metal droplet printing: (1) a nozzle with two or more orifices of varying diameter and length, (2) a set of corresponding pressure pulses that can eject droplets out of some, but not all, orifices in either magnetohydrodynamic (MHD-LMJ) or Pneumatic-LMJ, (3) the ability to change the pressure pulse on demand…
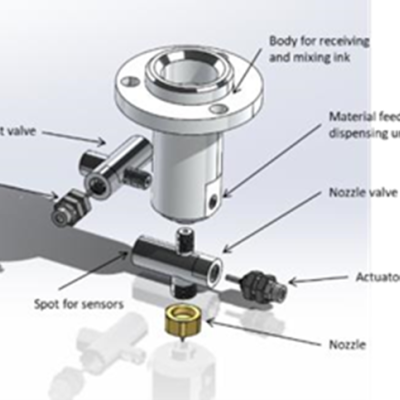
LLNL researchers’ approach to this challenge is to design a modular valve subsystem that redirects the flow away from the main nozzle to an “exhaust”. By re-routing the flow to a different exit port, steady state flow can be better maintained. The re-routing requires actuators that work in tandem; open and close of the nozzle and exhaust valves have to be executed simultaneously. …
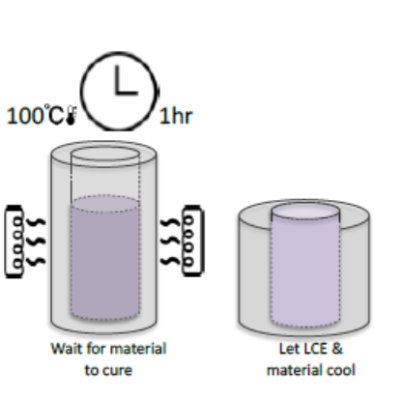
LLNL researchers developed novel workflows where material is first cast into the LCE molds at room temperature. Upon curing, the mold is induced to expand or contract (change shape) by external stimuli (light, heat, solvent) to self-release. A reduction to practice example used silica-loaded silicone ink casted into a LCE cylinder mold. It was cured at 100°C, and self-…
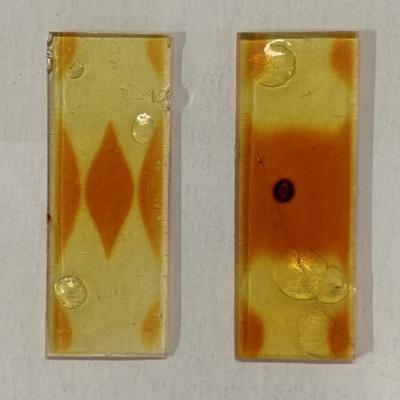
LLNL researchers have developed an innovative and uniform single-pot polymer multi-material system, based on a combination of 3 different reactive chemistries. By combining the three different constituent monomers, fine control of mechanical attributes, such as elastic modulus, can be achieved by adjusting the dosage of UV light throughout the additive manufacturing process. This…
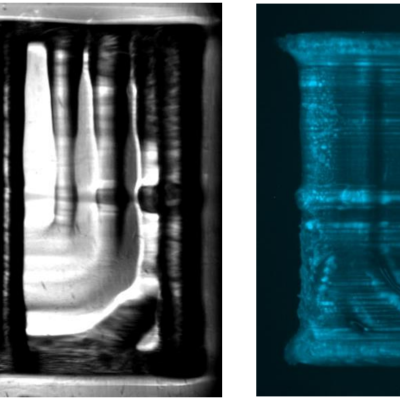
Three important aspects of this invention are: (1) the formulation of a photocurable resin containing a fluorophore that exhibits AIE behavior; (2) the method of in-situ and real-time characterization for monitoring the reaction kinetics during the photopolymerization and UV-curing process; and (3) the application of a new 3D steganographic ink for 3D encrypted structure.
Image Caption:…
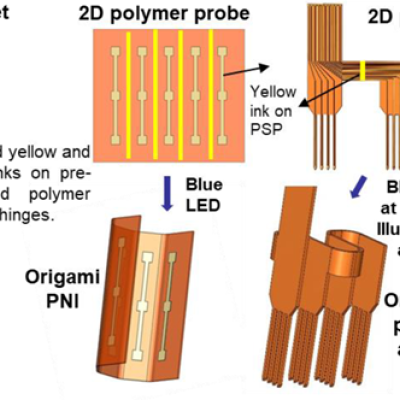
The approach involves 3D printing hinges made of Pre-Stressed Polymers (“PSP”) onto polyimide (“PI”) substrates. These hinges are then able to fold in response to externally applied stimuli, such as light. First, 2D PI devices will be microfabricated. Then, PSP infused with colored inks will be printed using Direct Ink Write (“DIW”) on the hinges of the PI devices. When…
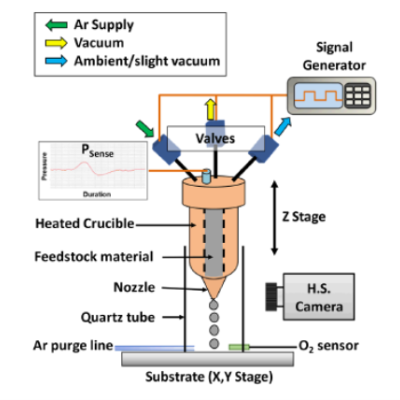
LLNL’s approach to meet this challenge is to use a pneumatic DOD-LMJ method wherein the nozzle is filled with a molten pure metal or metal alloy. There are two reservoirs in LLNL’s invention that are in direct contact with each other: the liquid metal reservoir that is constantly heated so the metal remains molten and an inert gas reservoir, which is connected to an inert gas pressure…
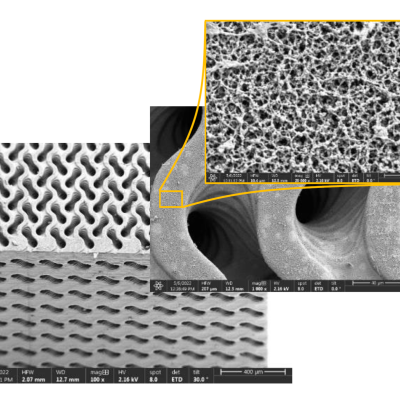
LLNL researchers have developed novel advanced manufactured biomimetic 3D-TPMS (triply periodic minimal surface) membrane architectures such as a 3D gyroid membrane. The membrane is printed using LLNL's nano-porous photoresist technology. LLNL’s 3D-TPMS membranes consist of two independent but interpenetrating macropore flow channel systems that are separated by a thin nano-porous wall…
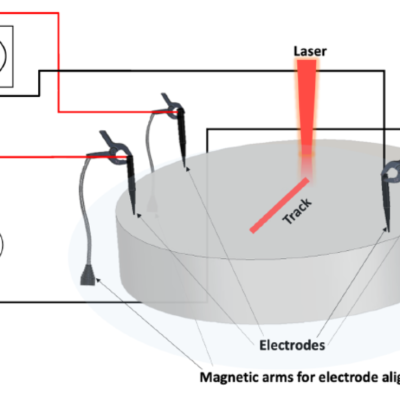
Electrodes that measure current and voltage are connected to the LPBF build plate by magnetic metal arms. These arms are placed on a steel weighted base that provides a high degree of mechanical flexibility to conform to small geometries and can be easily incorporated into a complex manufacturing system. Furthermore, the electrodes are connected to tapered copper tips that can…
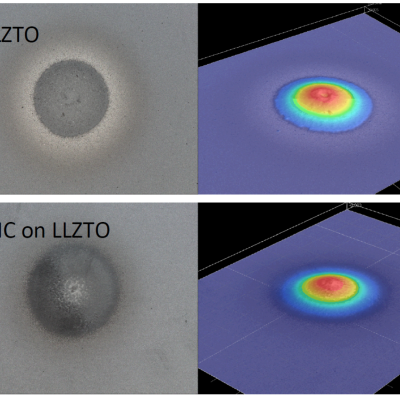
LLNL has co-developed a number of technologies thatuse cold spray deposition that enable new designs for functional materials with low waste.

The novel approach is to make Ultem® into an ink for DIW or droplet printing by dissolving Ultem® in solvents, such as tetrahydrofuran. This produces a viscous solvent-melt that is loaded into an ambient temperature extrusion system and deposited into a defined structure by the 3D printer. Solvent mobility is limited by the polymer structure, and further solvent removal allows…
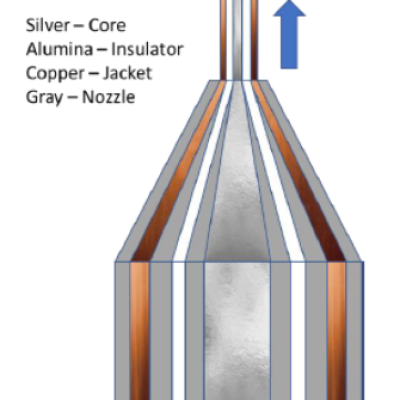
LLNL’s novel approach is to use Direct Ink Write (DIW) with a co-extrusion nozzle to enable the extrusion of multiple materials as one coil. With this method, LLNL researchers were able to produce an insulating wire that is composed of three different materials, axial conducting and insulating from its inner core to its outer sheath. After heat treatment, the printed wireI was then…
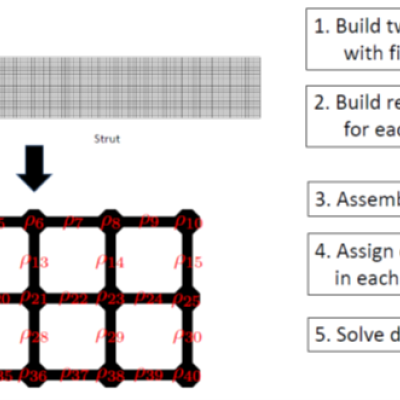
Beam Element-based Topology Optimization (“BETO”) is one of the conventional ways to design microstructures. It starts with an initial design that is composed of many beam elements. LLNL’s invention uses accurate Component-wise Reduced Order Models (“CWROM”) rather than the inaccurate beam elements. In doing so, the process becomes computationally efficient and fast, as each…
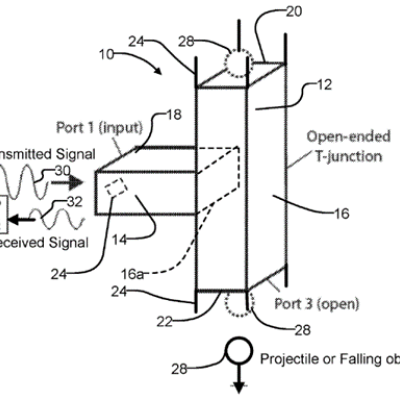
LLNL’s novel approach is to use waveguide-based devices and microwave energy to perform characterization of the projectile or droplet. Various embodiments of droplet devices can determine the size, motion (position, velocity, and acceleration), rate, and material elements of a moving element. This invention uses a tubular housing having a first end (input port) and a second end (…
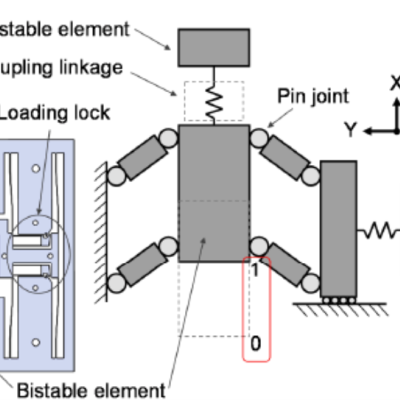
LLNL’s approach to designing logic gates uses heuristic as well as with the Freedom and Constraint Topologies (FACT) methods; these gates are then produced using existing additive manufacturing processes. The 10,122,365 and 10,678,293 patents describe how to fabricate the gates; the
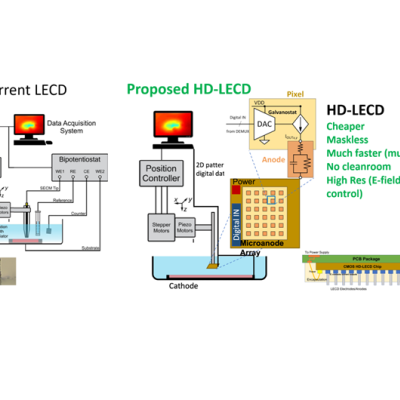
LLNL’s approach is to design and fabricate a massively-parallel microanode printhead using a custom complementary metal-oxide semiconductor integrated circuit (CMOS IC) chip with independent electronics for each pixel. This microanode in close proximity to the cathode surface will electroplate dissolved ions into a small voxel. The probe then moves and continues to deposit material…

LLNL researchers have developed an approach is to use pneumatic droplet ejection devices to rapidly 3D print solid metal parts that also have a smoother surface finish than conventional liquid metal printing. Pneumatic droplet ejection printers can be used in two different modes: “droplet mode” uses pulsed gas pressure to create individual droplets of liquid metal that are collected to…
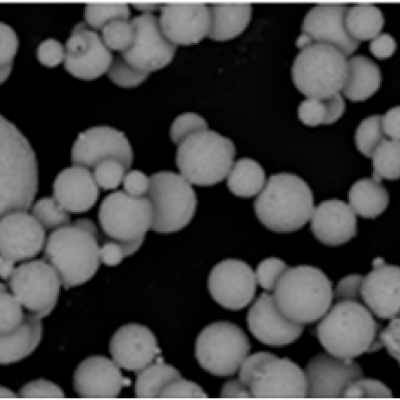
LLNL has developed a process to partially sinter starting material composed of smaller-sized powder particles to obtain a loose powder product that have larger-sized particles. To avoid the undesired formation of a single fully-sintered piece, the starting powder material is heated for a relatively shorter time. The time and temperature required for partial sintering is…
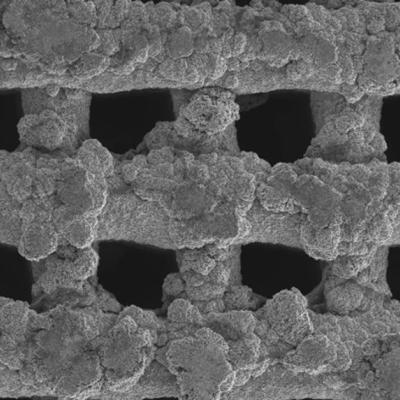
Improving the active material of the Zn anode is critical to improving the practicality of Zn-MnO2 battery technology. LLNL researchers have developed a new category of 3D structured Zn anode using a direct-ink writing (DIW) printing process to create innovative hierarchical architectures. The DIW ink, which is a gel-based mixture composed of zinc metal powder and organic binders, is…
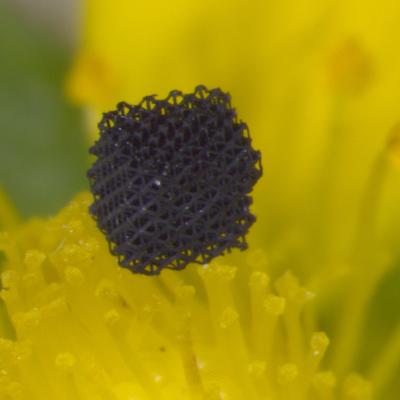
To overcome challenges that existing techniques for creating 3DGs face, LLNL researchers have developed a method that uses a light-based 3D printing process to rapidly create 3DG lattices of essentially any desired structure with graphene strut microstructure having pore sizes on the order of 10 nm. This flexible technique enables printing 3D micro-architected graphene objects with complex,…

The novel approach developed by LLNL researchers is to use an electric field as the non-contact-based powder remover. The main components of the remover are an electrode and a dielectric layer. As the remover moves across the stage, a high voltage is applied to the electrode that forms an electric field between the electrode and the powder bed. Under the influence of the…
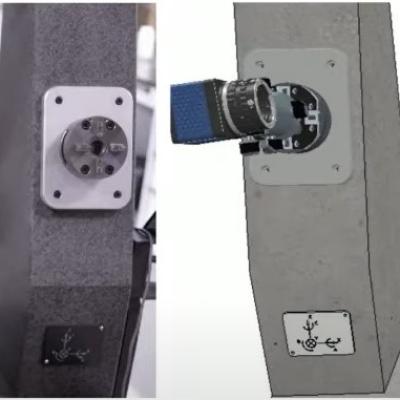
LLNL’s novel approach utilizes a number of techniques to improve reconstruction accuracy:
- Better coding scheme-based techniques
- Hardware-assisted techniques
- Adaptive fringe projection techniques
- Multi-exposure based techniques
The method requires specific calibration procedures and control of the hardware, which is achieved through a digital twin…
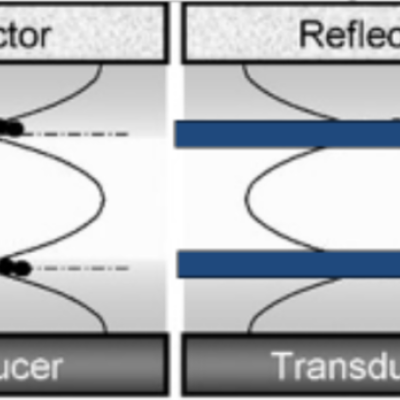
This novel AM approach utilizes cavitation bubbles generated within liquid resin by ultrasonic energy that trigger, induce, or catalyze a polymerization process (3D Ultrasound Polymerization). Ultrasound may be generated by piezoelectric transducers or high-power lasers and by modulating the ultrasound wave (frequency and amplitude), the cavitation site could be directed.

LLNL’s MVAM method comprises of a microwave applicator array coupled to a time-reversal beam steering algorithm to focus and deposit microwave energy in the feedstock material. The selective focusing of high-power microwave fields results in delivery of localized energy to arbitrary regions in a 3D volume. The localized area in the 3D volume heats up, allowing for the curing,…
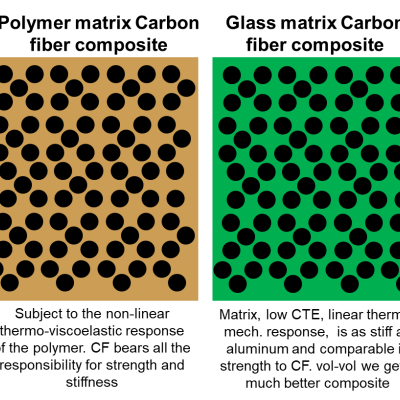
The approach is to combine the techniques of 3D printing aligned carbon fiber composites and melt-3D printing of glasses in a non-obvious manner to allow 3D printing (with controlled microstructure, fiber alignment, complex geometries, and advanced second order composite properties) of a new class of additively manufactured fiber-glass composites. It involves four major elements: …
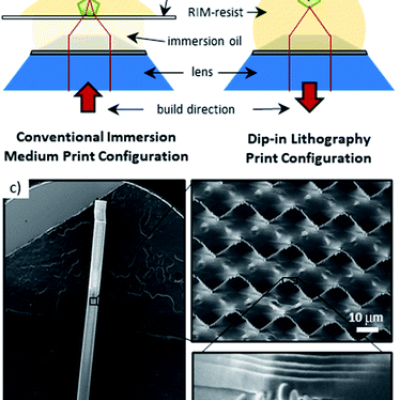
LLNL’s approach to producing refractive index matching (RIM) resin is to use a commercially available material known as polyhedral oligomeric silsesquioxane (POSS) precursors. To tune the refractive index, POSS can be functionalized with additives such as phenylthiol, until the refracted index match is achieved. For example, for a 1.4 NA oil objective lens, a RIM resin with a…
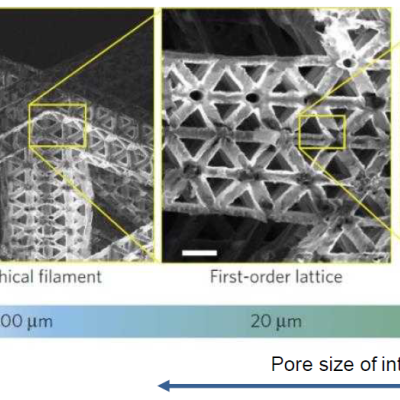
To get the best of both worlds – the sensitivity of LC-MS with the speed of PS-MS – and a functional substrate that can maintain sample integrity, LLNL researchers looked to 3D printing. They have patented a novel approach to create lattice spray substrates for direct ionization mass spectroscopy using 3D-printing processes.

LLNL researchers, through careful control over the chemistry, network formation, and crosslink density of the ink formulations as well as introduction of selected additives, have been successful in preparing 3D printable silicone inks with tunable material properties. For DIW (direct in writing) applications, LLNL has a growing IP portfolio around 3D printable silicone feedstocks for…
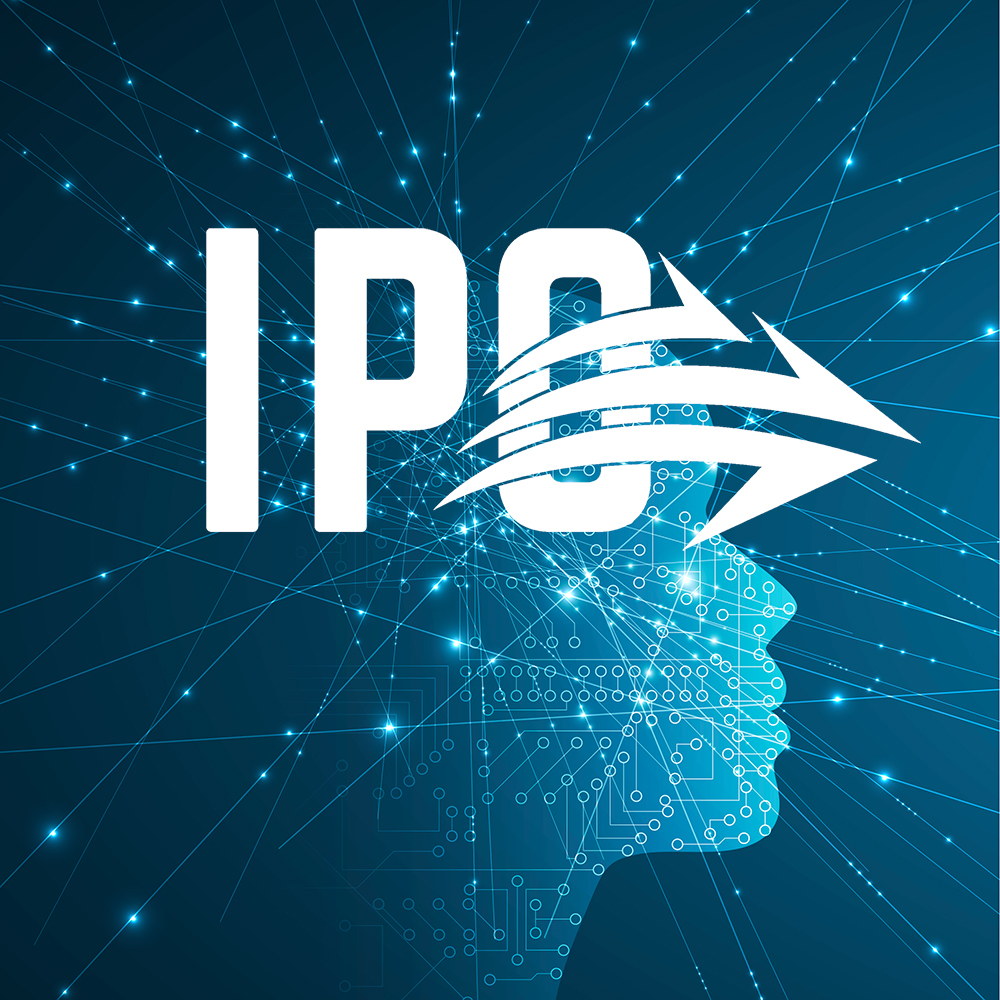
LLNL’s method of 3D printing fiber-reinforced composites has two enabling features:
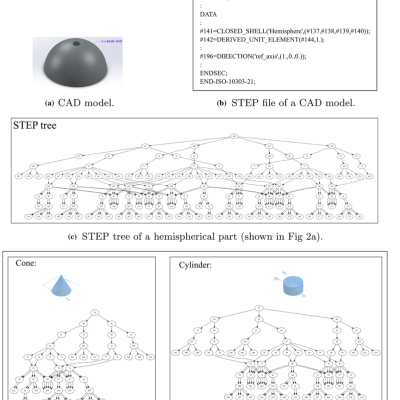
MBD captures the complete specification of a part in digital form and leverages (at least) the universal STEP file format. MBD has revolutionized manufacturing due to time and cost savings associated with containing all engineering data within a single digital source. LLNL researchers have been able to develop a novel encoding method to transform digital definitions in any given STEP file into…
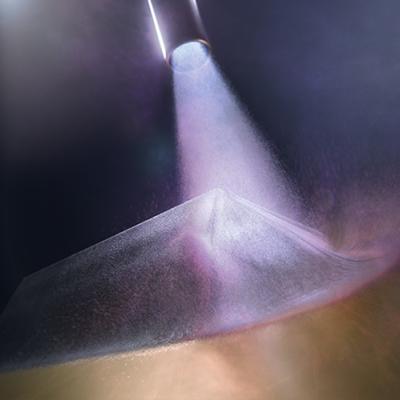
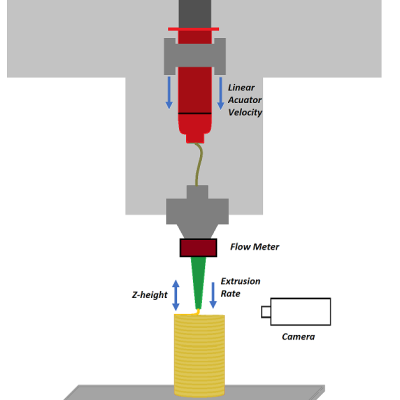
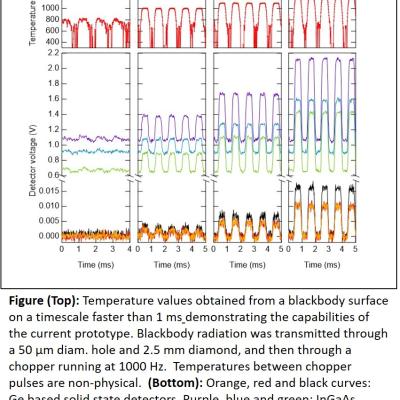
LLNL researchers have designed and tested performance characteristics for a multichannel pyrometer that works in the NIR from 1200 to 2000 nm. A single datapoint without averaging can be acquired in 14 microseconds (sampling rate of 70,000/s). In conjunction with a diamond anvil cell, the system still works down to about 830K.
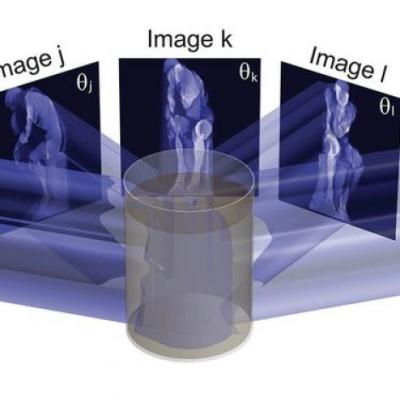
LLNL has developed a system and method that accomplishes volumetric fabrication by applying computed tomography (CT) techniques in reverse, fabricating structures by exposing a photopolymer resin volume from multiple angles, updating the light field at each angle. The necessary light fields are spatially and/or temporally multiplexed, such that their summed energy dose in a target resin volume…
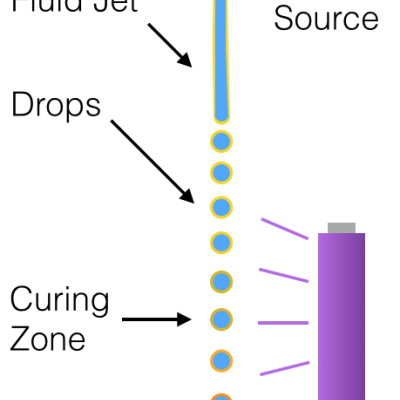
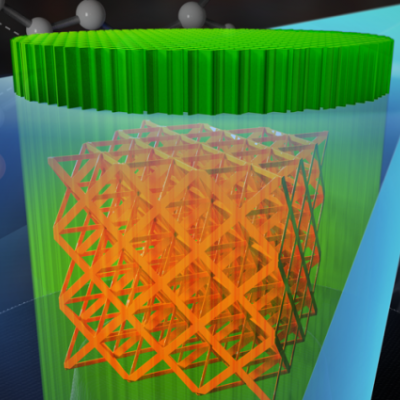
LLNL has solved the challenges of depth-resolved parallel TPL by using a temporal focusing technique in addition to the spatial focusing technique used in serial writing systems. We temporally focus the beam (through optical set-up design) so that a sharp Z-plane can be resolved while projecting 2D “light sheets” that cause localized photo-polymerization. This enables printing of complex 3D…
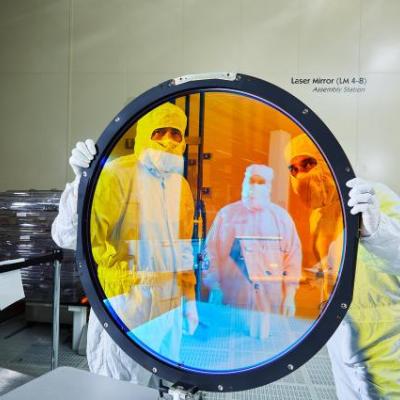
The LLNL method for optimizing as built optical designs uses insights from perturbed optical system theory and reformulates perturbation of optical performance in terms of double Zernikes, which can be calculated analytically rather than by tracing thousands of rays. A new theory of compensation is enabled by the use of double Zernikes which allows the performance degradation of a perturbed…
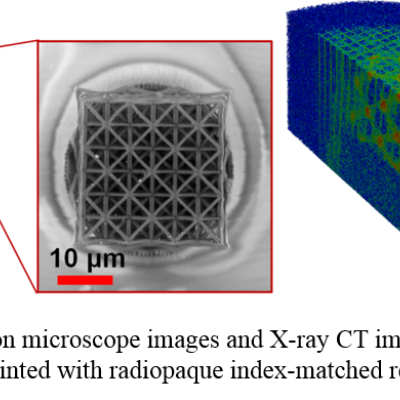
LLNL has developed an optically clear iodine-doped resist that increases the mean atomic number of the part. AM parts fabricated with this resist appear radio-opaque due to an increase in the X-ray attenuation by a factor of 10 to 20 times. Optical clarity is required so that the photons can penetrate the liquid to initiate polymerization and radio opacity is required to enable 3D computed…
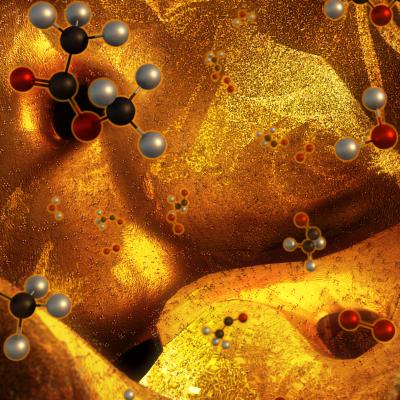
By combining 3D printing and dealloying., researchers at LLNL have developed a method for fabricating metal foams with engineered hierarchical architectures consisting of pores at least 3 distinct length scales. LLNL’s method uses direct ink writing (DIW), a 3D printing technique for additive manufacturing to fabricate hierarchical nanoporous metal foams with deterministically controlled 3D…
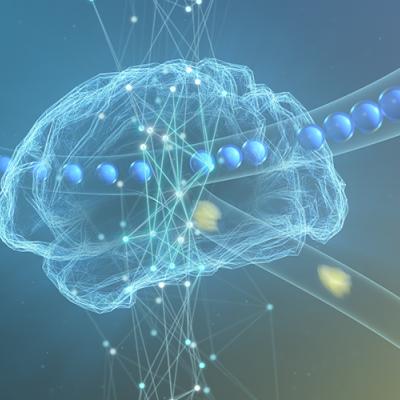
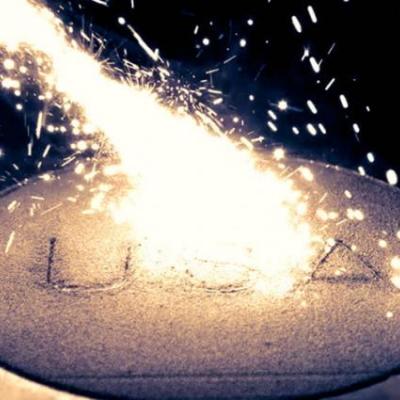
LLNL scientists have developed a new metal additive manufacturing technique that uses diode lasers in conjunction with a programmable mask to generate 2D patterns of energy at the powder surface. The method can produce entire layers in a single laser shot, rather than producing layers spot by spot as is currently done in powder bed fusion methods.
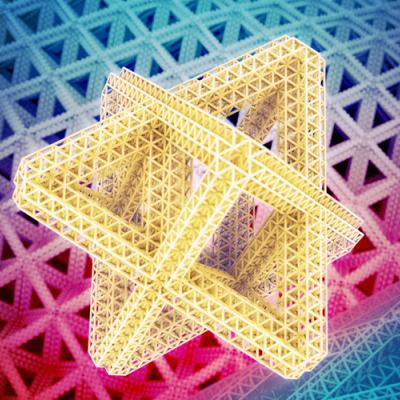